Unleashing the Power of Lean Six Sigma DMAIC: A Step-by-Step Guide to Process Improvement
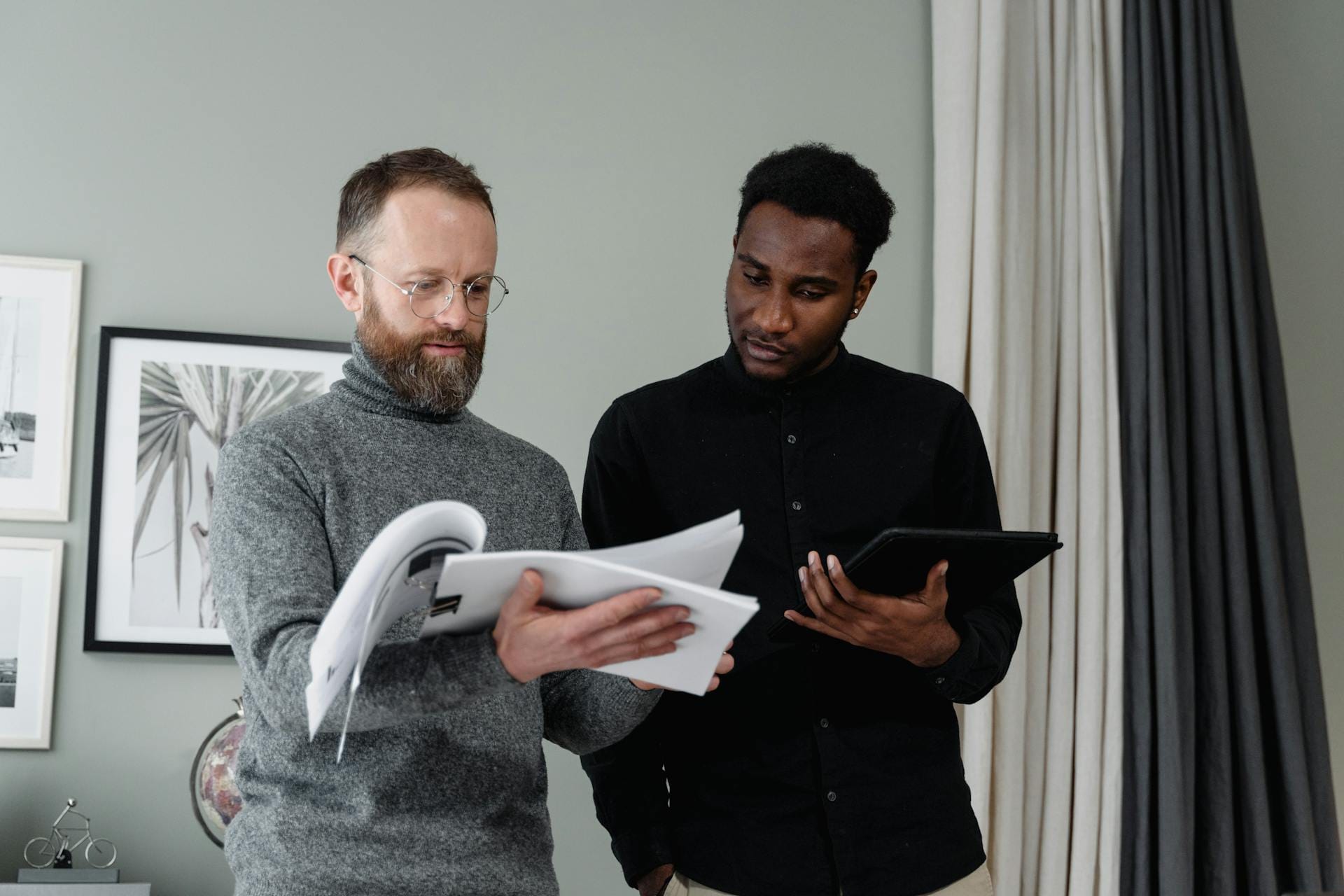
Unlock the potential of Lean Six Sigma DMAIC with our comprehensive step-by-step guide to process improvement. This article delves into each critical phase: Define, Measure, Analyze, Improve, and Control. Readers can expect a detailed exploration of methodologies and practical tips to enhance efficiency and quality in their processes. Whether you're new to Lean Six Sigma or looking to refine your skills, this guide offers valuable insights to drive impactful change in your organization.
Define Phase
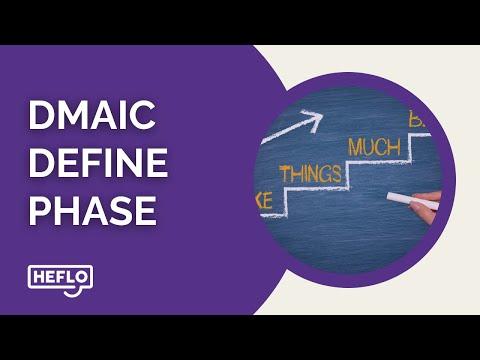
The Define Phase is the first step in the Lean Six Sigma DMAIC (Define, Measure, Analyze, Improve, Control) methodology. This phase sets the foundation for the entire process improvement project by clearly identifying the problem, setting objectives, and defining the scope of the project.
During the Define Phase, it is essential to create a project charter that outlines the problem statement, project goals, and key performance indicators (KPIs). This document serves as a formal agreement among stakeholders and provides a clear direction for the project team. Additionally, the project charter helps in securing the necessary resources and support from executive leadership.
Another critical activity in this phase is identifying the Voice of the Customer (VoC). Understanding customer needs and expectations is vital for ensuring that the process improvements align with customer requirements. Techniques such as surveys, interviews, and focus groups can be employed to gather this information.
Process mapping is also a significant component of the Define Phase. Creating a high-level map of the current process helps in visualizing the workflow and identifying key areas for improvement. Tools like SIPOC (Suppliers, Inputs, Process, Outputs, Customers) diagrams are often used to provide a comprehensive overview of the process.
For companies looking to document and automate their business processes, tools like HEFLO can be invaluable. HEFLO offers a cloud-based platform that simplifies the creation of process maps and ensures that all stakeholders have access to up-to-date process documentation.
Watch our latest video on business process documentation and discover how to transform your organization for maximum efficiency. Don't miss out – your path to better business starts here!
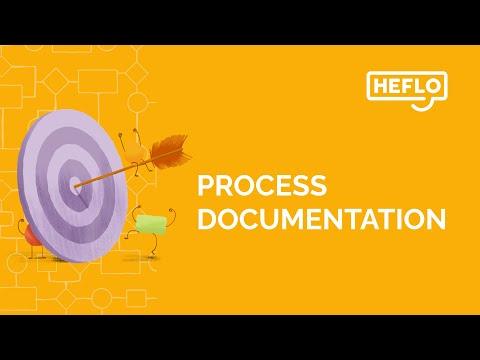
Finally, it is crucial to establish a project team with clearly defined roles and responsibilities. The team should include subject matter experts, process owners, and other key stakeholders who can contribute valuable insights and drive the project forward. Effective communication and collaboration among team members are essential for the success of the Define Phase.
Measure Phase
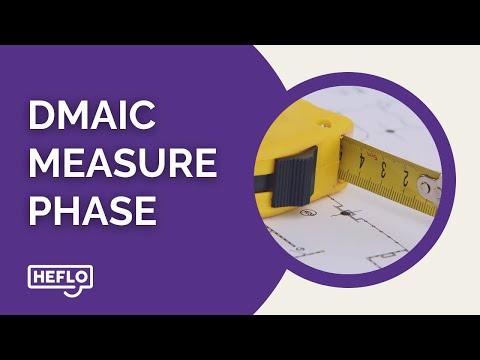
In the Lean Six Sigma DMAIC methodology, the Measure phase is where the foundation for data-driven decision-making is established. This phase focuses on quantifying the current performance of the process to identify areas of improvement. Accurate measurement is essential to understand the existing process capabilities and to set a baseline for future improvements.
Without data, you're just another person with an opinion. - W. Edwards Deming
During the Measure phase, various metrics are collected to provide a comprehensive view of the process performance. These metrics often include:
- Timeliness: Metrics such as throughput, cycle time, and delivery dates help in understanding the efficiency of the process.
- Product Quality: Metrics like defect rates, rework volume, and product reliability are crucial for assessing the quality of the output.
- Service Quality: Responsiveness, trustworthiness, and service reliability metrics provide insights into the customer experience.
- Cost: Labor cost, material cost, overhead, and cost of rework are measured to evaluate the financial impact of the process.
- Customer Satisfaction: Metrics that gauge whether the product or service meets customer expectations.
Collecting accurate data is critical in this phase. It involves using tools like Value Stream Mapping, Activity-Based Costing, and Statistical Process Control to monitor and control processes. These tools help in visualizing the value stream, understanding cost drivers, and maintaining statistical control over the process.
Performance measurement is not just about collecting data; it’s about ensuring that the data is accurate, complete, consistent, and timely. This phase often involves setting up real-time dashboards and performance measurement systems to provide ongoing insights into process performance. By integrating performance measurement into daily operations, companies can quickly identify issues and implement changes to optimize their processes.
For companies looking to document and automate their business processes, tools like HEFLO can be invaluable in the Measure phase of Lean Six Sigma DMAIC.
Analyze Phase
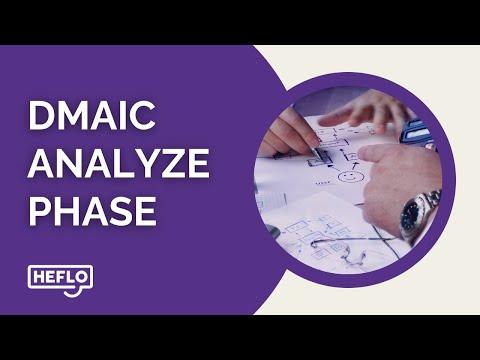
In the Analyze phase of the DMAIC methodology, the primary goal is to identify the root causes of process inefficiencies and defects. This phase involves a thorough examination of the data collected during the Measure phase to uncover patterns, correlations, and insights that can inform improvement strategies.
One of the initial steps in the Analyze phase is to choose the appropriate analytical frameworks and methodologies. There is no one-size-fits-all approach; the choice depends on the nature of the process and the available data. Formal methods such as Six Sigma and Lean provide a variety of tools and templates that can be extremely useful. For instance, tools like cause-and-effect diagrams, Pareto charts, and regression analysis are commonly employed to pinpoint problem areas.
It is often necessary to break down larger processes into smaller, more manageable sub-processes. This not only helps in managing complexity but also in showing progress to stakeholders. The analysis team should be cautious of "analysis paralysis," where over-analyzing can lead to delays and loss of interest among team members. To avoid this, the scope of analysis should be kept small and focused, ensuring that progress is visible and continuous.
Interviews with individuals from various business functions can provide valuable insights and help in making informed scope decisions. The more business functions and activities included in the analysis, the more complex and time-consuming it becomes. Therefore, it is crucial to balance the depth of analysis with the need for timely results.
Documentation is a key component of the Analyze phase. This includes an overview of the current business environment, the purpose of the process, a detailed process model, and identification of performance gaps. Additionally, the documentation should highlight redundancies that can be eliminated and provide recommended solutions. This serves as a formal agreement on the accuracy of the analysis and forms the basis for presenting results to management.
Daily team meetings can be beneficial for discussing findings and recognizing patterns. This collaborative approach ensures that all team members are aligned and can contribute to identifying opportunities for improvement. The analysis should also focus on the deliverables of the business unit or subprocess, ensuring that all work contributes to these deliverables.
Improve Phase
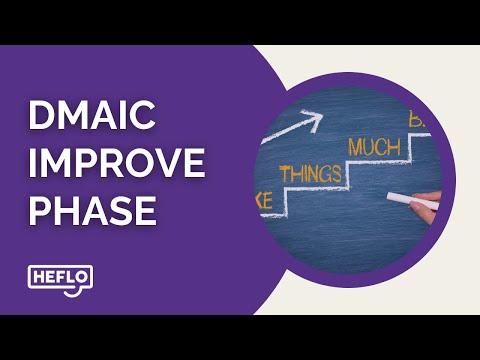
The Improve phase of the DMAIC (Define, Measure, Analyze, Improve, Control) methodology is where the actual transformation of processes takes place. This phase focuses on identifying, testing, and implementing solutions to the problems identified in the previous phases. The goal is to optimize processes to achieve better performance, quality, and efficiency.
During the Improve phase, teams brainstorm potential solutions and use various tools and techniques to identify the most effective improvements. Techniques such as brainstorming sessions, root cause analysis, and failure mode and effects analysis (FMEA) are commonly employed. These tools help in generating a wide range of ideas and in evaluating their potential impact on the process.
Once potential solutions are identified, they are tested through pilot runs or simulations. This step is crucial to ensure that the proposed changes will lead to the desired improvements without causing unintended consequences. Data collected during these tests are analyzed to verify the effectiveness of the solutions. Statistical tools and control charts are often used to compare the performance of the process before and after the implementation of improvements.
In addition to testing solutions, the Improve phase also involves refining and optimizing the process. This may include minimizing handoffs, ensuring that each action adds value to the process, and managing data or product inputs close to the source. The team reviews the process to ensure that all participants accurately execute the same best practice, driving process efficiency and effectiveness.
Finally, the team designs process controls and guidance to ensure the consistent execution of the improved process. This step is essential to reduce or eliminate variations, exceptions, and errors. By standardizing the improved process, organizations can achieve sustainable improvements and maintain high levels of performance over time.
Control Phase
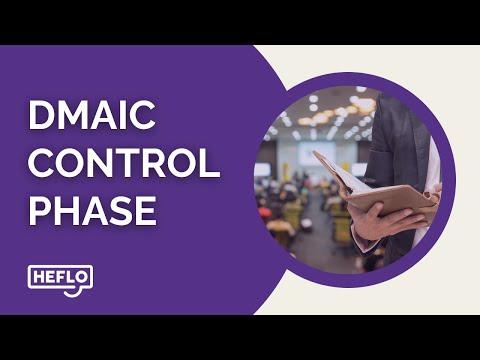
In the Lean Six Sigma DMAIC methodology, the Control Phase is dedicated to maintaining the improvements achieved during the previous phases. This phase ensures that the process changes are sustained over time and that the gains are not lost. It involves the implementation of control mechanisms and monitoring systems to keep the process within the desired performance levels.
Key Activities in the Control Phase
Several critical activities are undertaken during the Control Phase to ensure the stability and sustainability of the improved process:
- Develop Control Plans: A control plan is created to document the methods and metrics that will be used to monitor the process. This plan includes details on what needs to be measured, how often measurements should be taken, and who is responsible for the monitoring.
- Implement Monitoring Systems: Tools such as Statistical Process Control (SPC) charts are used to track process performance. These charts help in identifying any variations that may indicate a deviation from the desired process performance.
- Standardize Procedures: Standard operating procedures (SOPs) are updated or created to reflect the new process improvements. This ensures that all team members follow the same best practices, reducing variability and maintaining consistency.
- Training and Documentation: Training programs are conducted to educate employees about the new process changes and control mechanisms. Comprehensive documentation is also maintained to provide a reference for future process audits and reviews.
- Establish Response Plans: Response plans are developed to address any issues that may arise. These plans outline the steps to be taken if the process deviates from the control limits, ensuring quick and effective corrective actions.
Performance Metrics
Performance metrics play a crucial role in the Control Phase. These metrics help in assessing whether the process is performing as expected and meeting the set goals. Common performance metrics include:
- Timeliness: Measures such as throughput, cycle time, and delivery dates.
- Product Quality: Metrics like defect rates, rework volume, and product reliability.
- Service Quality: Indicators such as responsiveness, trustworthiness, and service reliability.
- Cost: Includes labor cost, material cost, overhead, and cost of rework.
- Customer Satisfaction: Evaluates whether the product or service meets customer expectations.
Continuous Improvement
The Control Phase is not just about maintaining the status quo; it also involves continuous improvement. By regularly reviewing performance data and feedback, organizations can identify new opportunities for enhancement and ensure that the process evolves to meet changing needs and conditions.
In conclusion, unleashing the power of Lean Six Sigma DMAIC offers a structured and effective approach to process improvement that can drive significant enhancements in quality, efficiency, and customer satisfaction. By meticulously following the Define, Measure, Analyze, Improve, and Control phases, organizations can identify root causes of inefficiencies, implement data-driven solutions, and sustain improvements over time. Embracing Lean Six Sigma DMAIC not only fosters a culture of continuous improvement but also equips teams with the tools and methodologies needed to achieve operational excellence and maintain a competitive edge in today's dynamic business environment.