How to Achieve Excellence: Unveiling Quality and Process Improvement Strategies
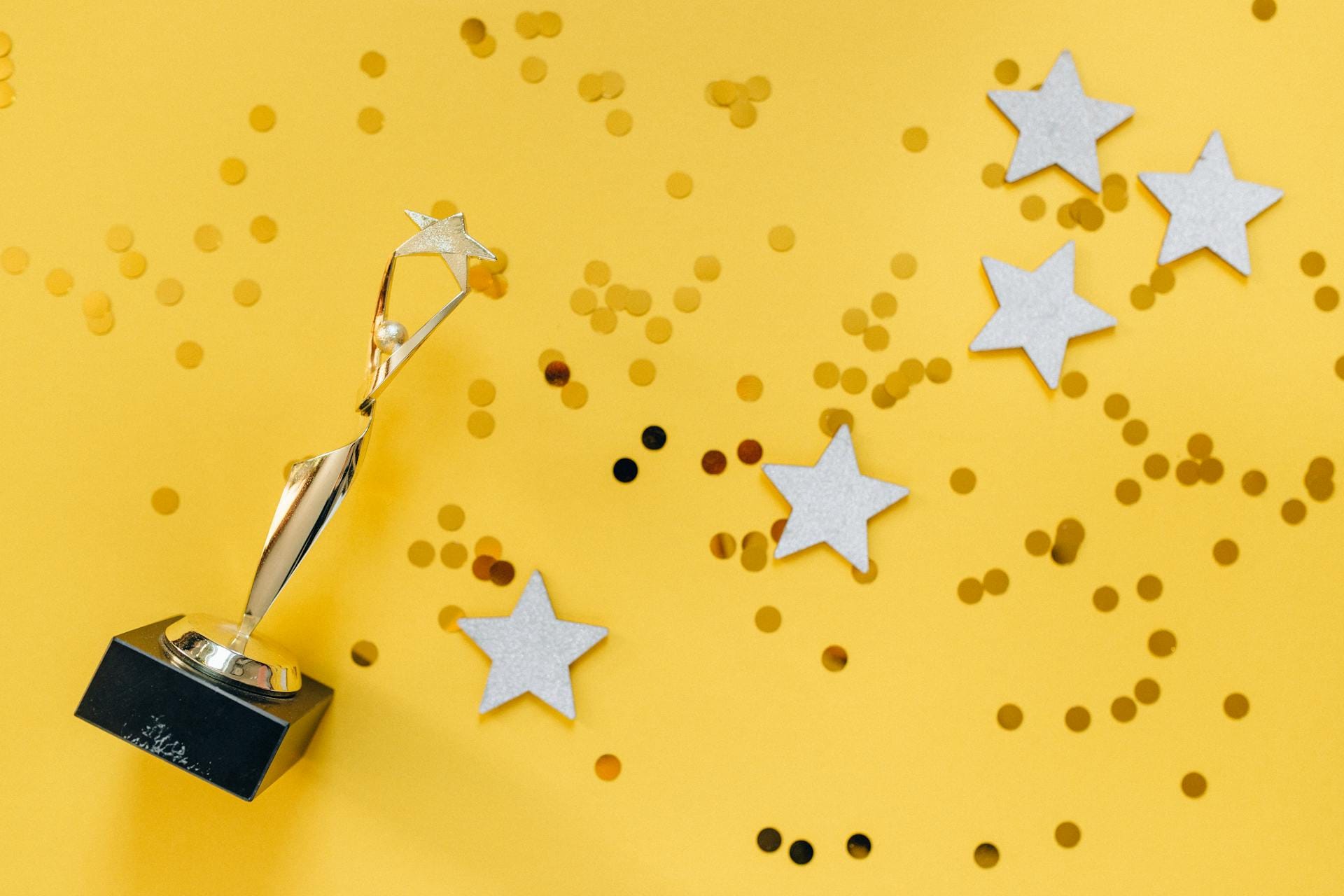
In the realm of business, excellence is not merely a goal but a continuous journey. Understanding what constitutes excellence is crucial for organizations aiming to thrive in competitive markets. This involves a multifaceted approach that encompasses quality, efficiency, and a deep understanding of customer needs.
Excellence in business can be defined as the consistent delivery of superior performance and value to customers, stakeholders, and employees. It involves not only meeting but exceeding expectations through continuous improvement and innovation. To achieve this, performance metrics are essential for measuring and managing business excellence. These metrics provide insights into how well processes are performing and where improvements are needed.
Key questions to consider include whether the process is meeting its performance goals, what the accepted service level for the process is, how to determine if the process has improved, and how business process monitoring is managed. Addressing these questions helps organizations maintain a clear view of their operational efficiency.
Additionally, continuous improvement is a cornerstone of business excellence. Regularly reviewing and refining processes to enhance performance is crucial, and techniques such as Six Sigma and Lean can be employed to identify inefficiencies and implement effective solutions.
Finally, understanding customer interactions with business processes is critical. Fewer required interactions generally lead to higher customer satisfaction. By focusing on these areas, organizations can create a seamless experience that not only meets but exceeds expectations.Key questions to address include:
- Who is the customer?
- How do customers interact with the process?
- Are customers satisfied with the process?
Key Principles of Quality Management
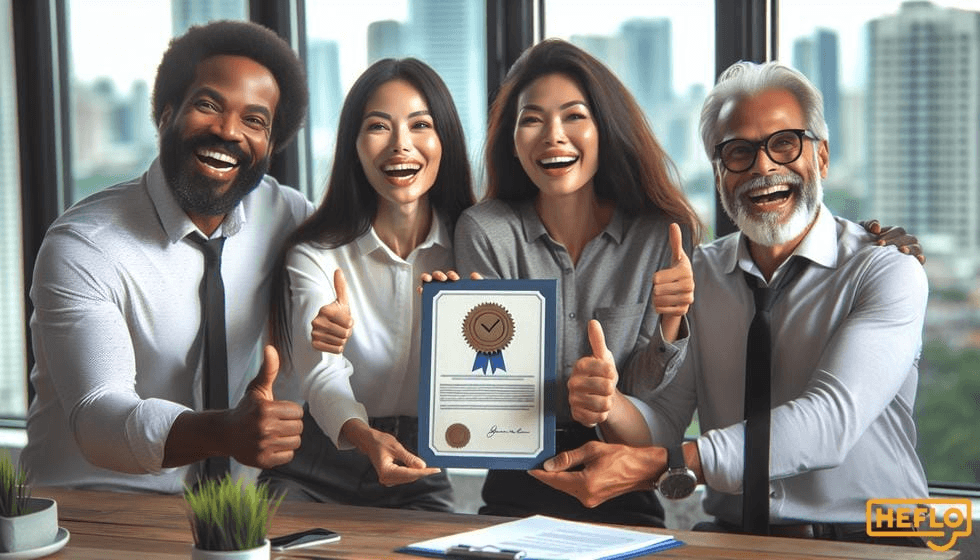
Quality management is a critical aspect of any organization aiming to deliver superior products and services. It involves a systematic approach to ensuring that all activities within a business are efficient and effective in meeting customer requirements. The key principles of quality management provide a framework for organizations to achieve consistent quality and continuous improvement.
Quality is not an act, it is a habit. Aristotle
Customer Focus
Understanding and meeting customer needs is the cornerstone of quality management. Organizations must strive to exceed customer expectations by delivering products and services that provide value. This involves gathering customer feedback, analyzing their requirements, and incorporating their needs into the product development and service delivery processes.
Leadership
Strong leadership is essential for establishing a unified direction and purpose within an organization. Leaders must create an environment where employees are motivated to achieve the organization's quality objectives. This includes setting clear goals, providing necessary resources, and fostering a culture of continuous improvement.
Watch the video below to understand the different types of leadership.
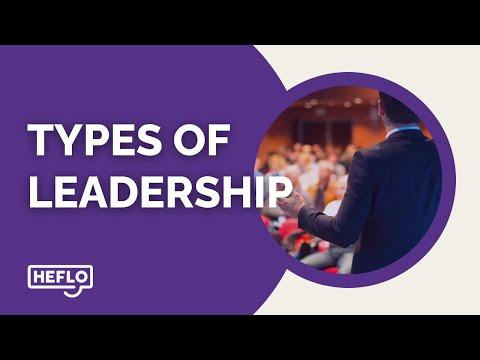
Engagement of People
Employees at all levels are the backbone of an organization. Their full involvement enables their abilities to be used for the organization's benefit. Engaging employees involves providing training, encouraging open communication, and recognizing their contributions to quality improvement.
Process Approach
Managing activities and resources as processes helps ensure consistent and predictable results. A process approach involves understanding how processes interrelate, identifying areas for improvement, and optimizing processes to enhance efficiency and effectiveness.
Continuous Improvement
Continuous improvement should be a permanent objective of the organization. This involves regularly reviewing processes, identifying areas for enhancement, and implementing changes to improve performance. Techniques such as Six Sigma and Lean can be employed to drive continuous improvement efforts.
Evidence-Based Decision Making
Decisions should be based on the analysis of data and information. By using accurate and reliable data, organizations can make informed decisions that lead to better outcomes. This involves collecting relevant data, analyzing it to identify trends and patterns, and using the insights to guide decision-making processes.
Relationship Management
Organizations must manage their relationships with interested parties, such as suppliers and partners, to optimize performance. Effective relationship management involves collaborating with stakeholders, understanding their needs, and working together to achieve mutual benefits.
Monitoring and Controlling Operations
It is crucial to continually measure, monitor, and control processes to achieve desired results. This involves setting performance metrics, regularly reviewing them, and making necessary adjustments to ensure processes remain in control. Monitoring tools and dashboards can help track performance and identify deviations that need to be addressed.
Process Improvement Methodologies
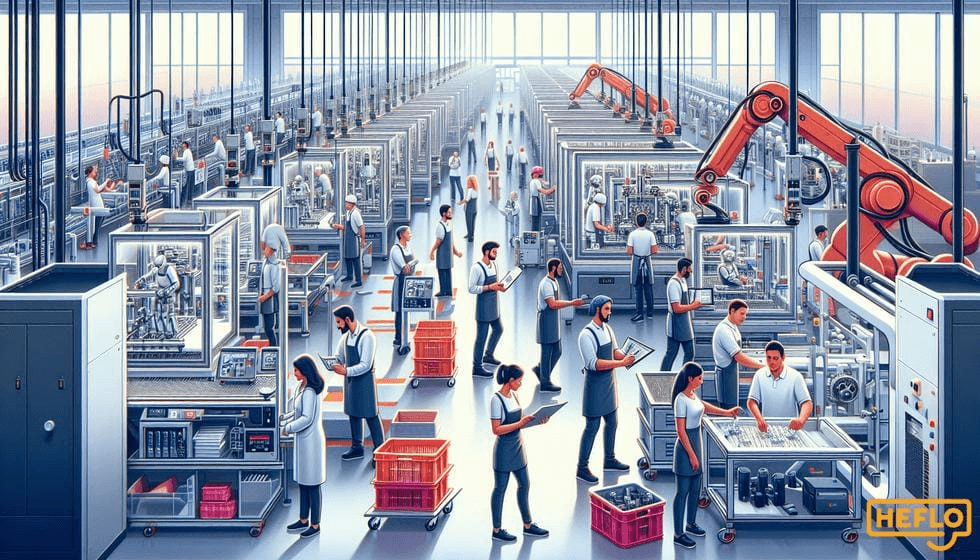
Process improvement methodologies are essential for organizations aiming to enhance efficiency, reduce waste, and deliver higher quality products and services. These methodologies provide structured approaches to analyze, redesign, and optimize processes, ensuring that every step adds value and aligns with organizational goals.
Lean
Lean methodology focuses on minimizing waste and maximizing value. It involves identifying non-value-adding activities and eliminating them to streamline processes. Techniques such as Value Stream Mapping help visualize the flow of materials and information, making it easier to spot inefficiencies.
Six Sigma
Six Sigma aims to improve process quality by identifying and removing the causes of defects and minimizing variability. It uses statistical methods and a structured DMAIC (Define, Measure, Analyze, Improve, Control) approach to achieve near-perfect quality levels.
Watch the video below to learn more on Six Sigma.
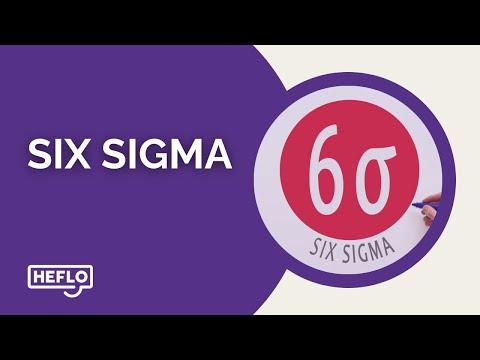
DMAIC
DMAIC is a data-driven improvement cycle used for optimizing and stabilizing business processes. Each phase focuses on specific activities:
- Define: Identify the problem and project goals.
- Measure: Collect data and determine current performance.
- Analyze: Identify root causes of defects.
- Improve: Implement solutions to address root causes.
- Control: Monitor the process to ensure continued performance.
Watch our video on DMAIC to master this topic.
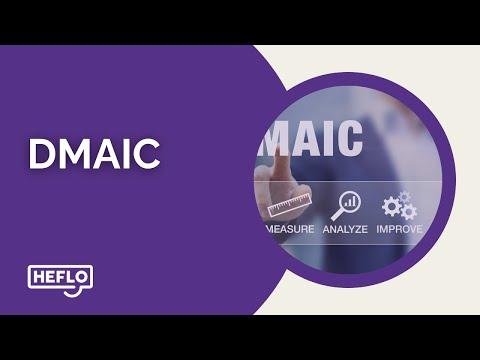
Continuous Process Improvement (CPI)
Continuous Process Improvement is an ongoing effort to enhance products, services, or processes. It involves regular assessment and incremental improvements, fostering a culture of constant enhancement.
Kaizen
Kaizen, a Japanese term meaning "change for better," is a CPI approach that encourages small, continuous improvements. It involves all employees, from top management to frontline workers, in identifying opportunities for improvement.
Reengineering
Reengineering involves fundamentally rethinking and redesigning business processes to achieve dramatic improvements in critical performance measures such as cost, quality, service, and speed. It often requires a radical change in organizational structures and workflows.
Technology-Enabled BPM
Business Process Management (BPM) leverages technology to model, analyze, and optimize processes. BPM tools provide a platform for automating workflows, monitoring performance, and ensuring compliance with best practices.
Performance Metrics
Performance metrics are essential for monitoring and controlling operations. They provide actionable insights into how well processes are performing and where improvements are needed. Key metrics might include turnaround times, defect rates, and customer satisfaction levels.
Also, continual measurement and monitoring are crucial for maintaining process control. By regularly reviewing performance metrics and dashboards, organizations can quickly identify deviations and take corrective actions to ensure processes remain aligned with goals.
Customer Focus and Satisfaction
Companies that prioritize their customers' needs and continuously strive to enhance their satisfaction levels are more likely to achieve long-term success.
The customer is always right. Harry Gordon Selfridge
Understanding Customer Needs
To truly focus on customers, it is essential to understand their needs and expectations. This involves gathering feedback through various channels such as surveys, focus groups, and direct interactions. By doing so, companies can gain valuable insights into what their customers value most and identify areas for improvement.
Customer Interactions
Understanding customer interactions with your processes is critical. Fewer required interactions generally lead to higher customer satisfaction. Key questions to consider include:
- Product Launch Variance: Measuring the deviation between planned and actual product launch dates to identify areas for improvement.
Forecast Accuracy: Ensuring that demand forecasts are accurate to optimize inventory levels and reduce stockouts or overstock situations.Who is the customer? - How many times does a customer interact with the process?
- Are there redundancies in the interactions?
- What suggestions do customers have for improving the process?
Feedback and Monitoring
Most companies have some form of performance monitoring and reporting. However, it is crucial to measure the right things. Regularly reviewing performance metrics and dashboards ensures that processes are accurately measured and monitored, allowing for timely adjustments to enhance customer satisfaction.
Watch the video below to understand how to receive and manage customer feedback using the concept of Net Promoter Score.
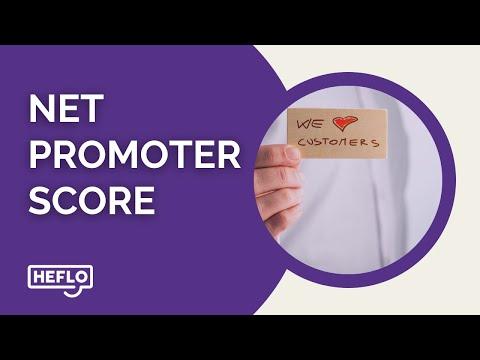
Future Trends in Quality and Process Improvement
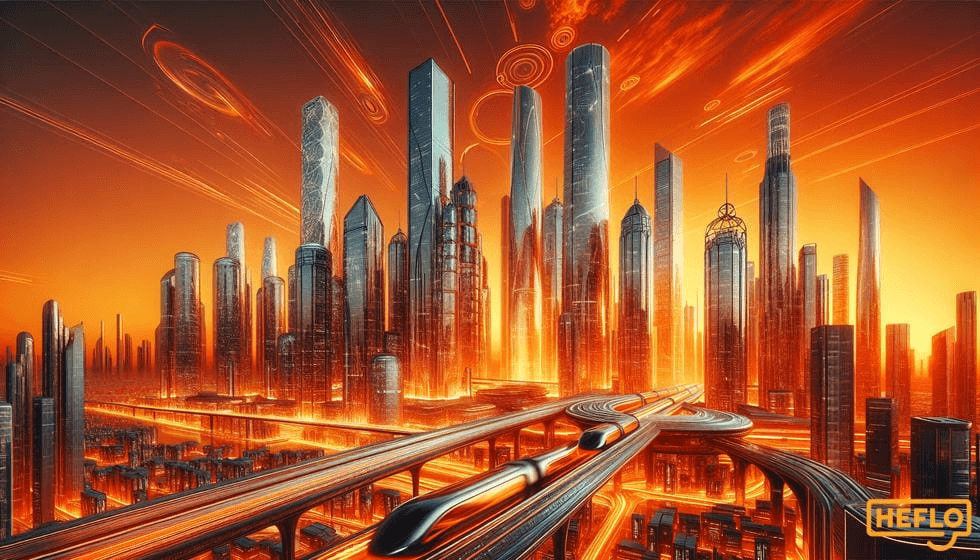
The landscape of quality and process improvement is continuously evolving, driven by technological advancements, changing market dynamics, and the increasing demand for efficiency and excellence. Organizations must stay ahead of these trends to maintain a competitive edge and achieve sustainable growth.
Integration of Artificial Intelligence and Machine Learning
Artificial Intelligence (AI) and Machine Learning (ML) are revolutionizing quality and process improvement. These technologies enable predictive analytics, which can foresee potential issues before they arise, allowing for proactive measures. AI-driven tools can analyze vast amounts of data to identify patterns and anomalies, providing insights that were previously unattainable.
For instance, AI can enhance product launch variance and forecast accuracy by analyzing historical data and market trends. This leads to more precise planning and execution, reducing the risk of errors and improving overall quality.
Real-Time Monitoring and Control
Continuous monitoring and control of operations are becoming more sophisticated with the advent of IoT (Internet of Things) and advanced sensor technologies. These tools provide real-time data on process performance, enabling immediate adjustments and improvements. Watch the video below for more on IoT.
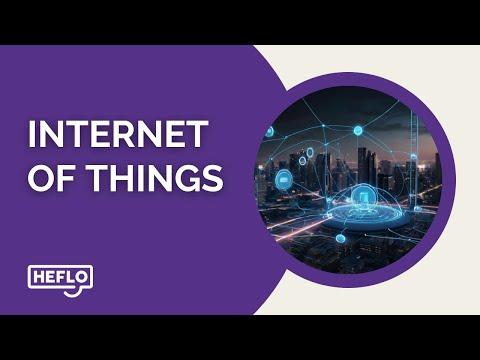
Organizations can now implement real-time dashboards that display key performance metrics, allowing for instant identification of deviations and prompt corrective actions. This approach ensures that processes remain within desired parameters, enhancing efficiency and quality.
Enhanced Customer Interactions
As said before, understanding and improving customer interactions is critical for process success. Future trends emphasize reducing the number of required interactions between customers and services, thereby increasing customer satisfaction.
Advanced CRM (Customer Relationship Management) systems integrated with AI can provide deeper insights into customer behavior and preferences. This information helps in tailoring processes to meet customer needs more effectively, resulting in higher satisfaction and loyalty.
Continuous Improvement and Agile Methodologies
Continuous improvement remains a cornerstone of process optimization. The adoption of agile methodologies allows organizations to be more flexible and responsive to changes. This approach involves iterative cycles of planning, executing, and reviewing, which helps in identifying improvement opportunities more frequently.
Techniques like Six Sigma and Lean are being integrated with agile practices to create a robust framework for ongoing process enhancement. This combination ensures that quality improvements are not only sustained but also accelerated.
Data-Driven Decision Making
The future of quality and process improvement is heavily reliant on data-driven decision making. Organizations are increasingly leveraging big data analytics to gain actionable insights into their operations. This approach involves collecting and analyzing data from various sources to make informed decisions that drive process improvements.
By using data analytics, companies can identify performance gaps, understand the root causes of issues, and implement targeted solutions. This leads to more efficient processes and higher quality outcomes.
In conclusion, achieving excellence is a multifaceted journey that hinges on the continuous pursuit of quality and the strategic implementation of process improvement. By embracing a culture of constant evaluation and refinement, organizations can not only meet but exceed their goals, fostering an environment where excellence becomes the norm. The integration of these strategies ensures that every aspect of the operation is optimized, leading to sustainable success and a competitive edge in the marketplace. Ultimately, the commitment to quality and process improvement is the cornerstone of any thriving organization, paving the way for innovation, efficiency, and unparalleled performance.