Transformative Business Process Redesign Examples That Drive Results
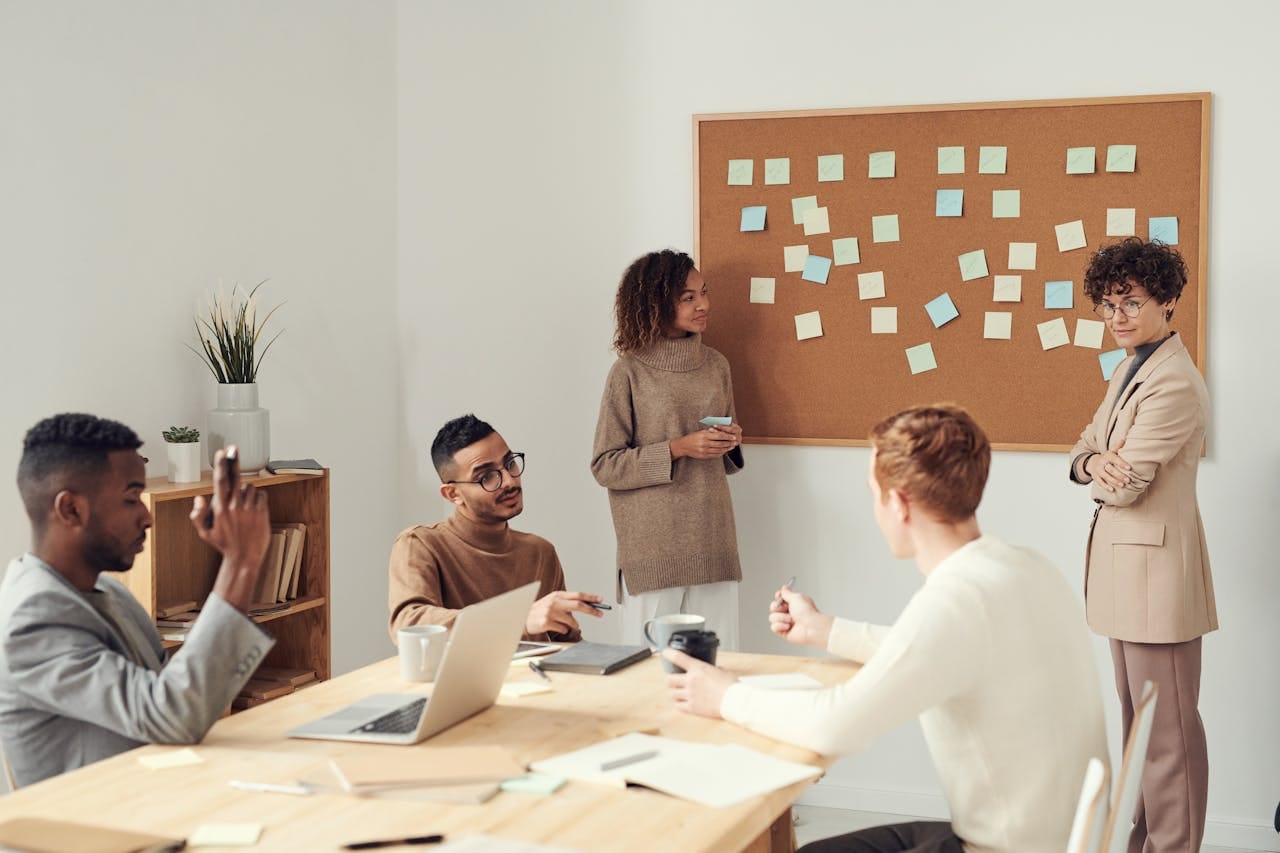
Real-world examples of business process redesign involve fundamentally rethinking and radically redesigning core business processes to achieve dramatic improvements in critical measures of performance, such as cost, quality, service, and speed, often leveraging methodologies like ESOAR.
Key Takeaways
- Business Process Redesign (BPR) aims to dramatically improve efficiency, cut costs, enhance quality, and boost satisfaction by rethinking core processes.
- Capgemini's ESOAR methodology (Eliminate, Standardize, Optimize, Automate, Robotize) provides a structured approach, addressing root causes before applying technology.
- Eliminating waste and unnecessary steps often yields the most significant initial gains.
- Standardizing processes across units or regions is crucial for consistency and effective automation.
- Optimizing existing technology (like ERPs) can provide quick wins and maximize current investments.
- Automation and Robotization (RPA) deliver substantial efficiency improvements when applied strategically to well-defined processes.
- Successful BPR initiatives deliver quantifiable results, including significant time savings, cost reductions, efficiency percentage increases, and improved compliance.
- BPR impacts are seen across various functions like Finance, HR, Supply Chain, and Customer Service.
🎙️ Tune in to our podcast for the full breakdown of these business process redesign examples — straight from the experts!
What are Real-World Examples of Business Process Redesign?
Understanding Business Process Redesign (BPR)
Business Process Redesign (BPR) is the fundamental rethinking and radical redesign of business processes to achieve dramatic improvements in critical, contemporary measures of performance, such as cost, quality, service, and speed. It's not about making minor tweaks or incremental improvements; it's about stepping back, questioning existing assumptions, and finding entirely new ways to organize work and deliver value.
The primary goals of BPR typically include:
- Improving Efficiency: Streamlining workflows to get things done faster and with fewer resources.
- Reducing Costs: Eliminating wasteful activities, redundancies, and unnecessary overhead.
- Enhancing Quality: Reducing errors, improving accuracy, and ensuring consistency in outputs.
- Boosting Customer/Employee Satisfaction: Creating smoother, faster, and more user-friendly experiences for both external customers and internal employees.
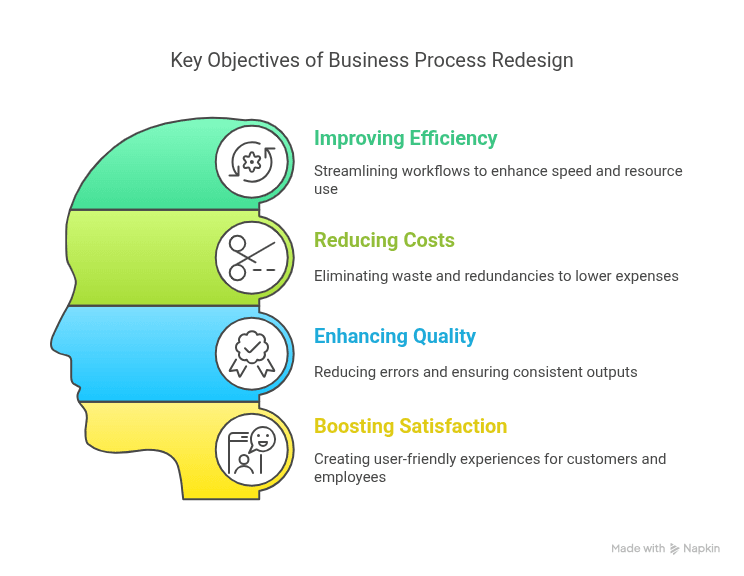
Introducing the ESOAR Methodology for Process Redesign
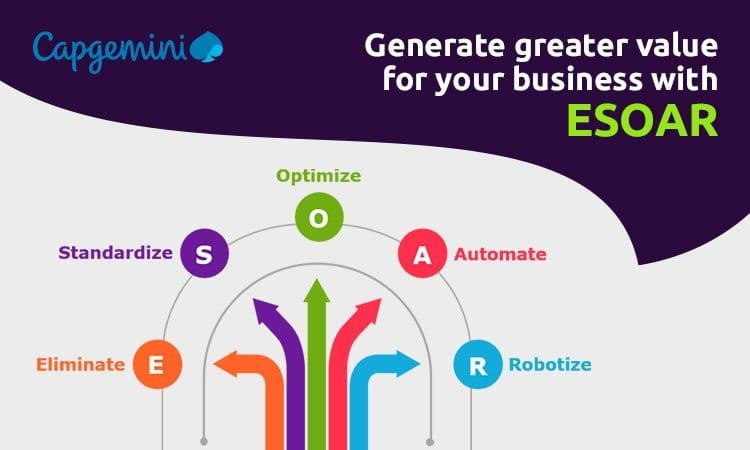
A powerful framework for approaching BPR, particularly when considering automation, is Capgemini's ESOAR (Eliminate, Standardize, Optimize, Automate, Robotize) methodology. This unique and straightforward transformation approach is designed to develop intelligent automation solutions by first addressing the underlying causes of inefficiency before tackling the symptoms.
The purpose of ESOAR is to reimagine business processes effectively, enabling straight-through processing and ensuring that automation efforts deliver maximum impact with minimal expenditure. It provides a foundational step towards intelligent automation and AI, ensuring that organizations don't simply automate broken or inefficient processes.
1. Eliminate
The crucial first step is to Eliminate all unnecessary steps, waste, and redundancy within a process. This involves identifying and removing activities that add no value, are duplicated elsewhere, or are simply obsolete. The focus is on defining the most efficient "golden path" for a process and refusing to design solutions for tasks or exceptions that fall outside this optimal flow. This includes eliminating redundant transactions, overlapping processes, and activities impacting time, cost, and effort.
2. Standardize
Once waste is removed, the next step is to Standardize the remaining process steps. This involves creating consistent "golden paths" that are validated by the business based on factors like customer experience, effectiveness, business value, and efficiency. Standardization limits unnecessary customization and variation, ensuring that processes are performed consistently across different teams, locations, or scenarios. This applies to standardizing inconsistent processes and the basics of transactions and interactions.
3. Optimize
With a standardized process, the focus shifts to Optimize. This involves improving the existing process and making the best use of current technology investments, such as Enterprise Resource Planning (ERPs) systems and workflow tools. Optimization aims to repurpose existing assets, enhance the IT landscape supporting the process, optimize tasks and documentation, and create better alignment of purpose among stakeholders, often leading to quick wins.
4. Automate
Only after eliminating, standardizing, and optimizing should Automate be seriously considered. This step involves applying best-of-breed automation tools and new AI solutions to the streamlined, standardized processes. The goal is to automate tasks where technology excels, freeing up human effort to focus on higher-value activities, judgment-based decisions, and areas where they can best impact outcomes.
5. Robotize
Finally, Robotize involves using technologies like Robotic Process Automation (RPA) for highly repetitive, rule-based, and time-consuming tasks that are often invisible to the end customer or user. RPA bots can efficiently handle data entry, transfers, reconciliations, and report generation behind the scenes, further improving the efficiency and effectiveness of the overall redesigned process.
Business Process Redesign Examples by Function & Industry
The ESOAR methodology has been successfully applied across various functions and industries, delivering tangible results. Here are several real-world business process redesign examples:
Finance and Accounting Redesign Examples
Major Manufacturing Client (Shared Service F&A)
Challenge: This client believed their existing SAP implementation was performing well but engaged Capgemini to identify practical improvements for their shared service finance and accounting operations.
Redesign Steps:
- Eliminate: Removed redundant process steps like the need to print hard copies.
- Standardize: Harmonized processes across different countries served by the shared service center.
- Optimize: Improved the utilization of their existing SAP system and other related applications.
- Automate: Implemented automation for data transfer to the reporting module and automated the creation and routing of dispute cases.
- Robotize: Used RPA for tasks like preparing trial balance review packages, transferring data where interfaces didn't exist, consolidating dispute data, transferring invoice data, and generating vendor account check lists.
Key Outcomes: Achieved a 25% improvement in payment on time, a 30% increase in invoice processing efficiency, and a 50% increase in payment process efficiency. User satisfaction rose by 15 points, control over processes improved, and the effort required decreased, demonstrating significant value derived from optimizing existing platforms.
▶️ Watch our latest video on Shared Services Centers and see how they transform operations!
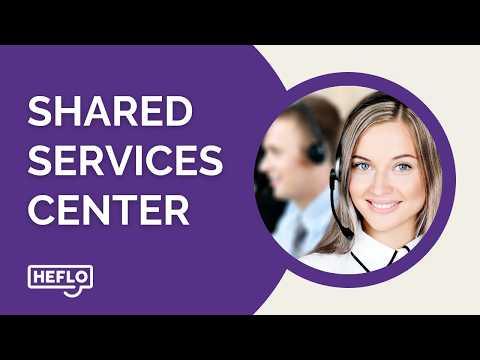
Global FMCG Company (Finance and Accounting)
Challenge: Aiming for best-in-class digital finance processes, this company faced challenges despite having standard processes based on Capgemini’s Global Process Model (GPM), as many steps still relied on manual inputs.
Redesign Steps:
- Eliminate: Removed redundant processes (while maintaining controls), implemented thresholds for journals and sundry invoicing, and rationalized banking relationships.
- Standardize: Enforced standard templates and formats, ensured GPM adherence across locations, and implemented structural initiatives like inter-company hub centralization.
- Optimize: Leveraged SAP HANA T-Codes, improved intercompany workflows, implemented auto-certification for sub-ledger reconciliation, automated bank statement uploads, and optimized costs through location mix.
- Automate: Introduced a Forex automation tool, enhanced Trintech for reconciliations, automated bank statement delivery and auto-mailer communications, and implemented a proactive product costing process.
- Robotize: Used RPA for processing fixed asset and sundry invoicing requests, validating journal templates logically, and preparing/uploading reconciliations.
Key Outcomes: Resulted in end-to-end process integration with enhanced visibility. Standardized procedures and "golden rules" were established, leading to a lower cost of compliance through automated controls. A significant 44% effort reduction was achieved in key areas like account reconciliation, fixed assets, bank reconciliation, and intercompany processes.
Credit-to-Cash Process Redesign Example
Large Retailer (Credit-to-Cash)
Challenge: Following a change in lockbox providers, the retailer experienced sub-optimal auto match rates (AMR) for electronic payments, impacting cash application efficiency.
Redesign Steps:
- Eliminate: Removed several manual steps required to review data in secondary bank reports.
- Standardize: Standardized previously fluid process stages and critical data elements required for auto-matching receipts.
- Optimize: Enhanced existing technology to import secondary bank data directly into their platform, increasing the data hit rate for matching. (Note: Automation focused on optimizing existing tech).
- Automate: In this specific case, the "Automate" step was achieved through optimization of existing technology rather than introducing new automation tools.
- Robotize: Implemented RPA to handle the transfer of necessary data into the system.
Key Outcomes: The redesign led to a significantly improved AMR, resulting in faster, more efficient, and effective cash application. This, in turn, contributed to an improved Days Sales Outstanding (DSO). This case highlights ESOAR's flexibility in targeting specific process elements.
🤖 Discover how RPA is changing the game! Watch our video on Robotic Process Automation and unlock new levels of efficiency.
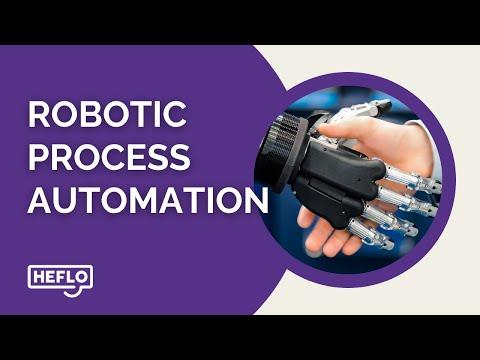
Human Resources Redesign Examples
Major Multinational Engineering Company (HR Employee Support)
Challenge: Needed to establish a new, standardized global HR operating model to support the launch of the Workday platform from a new centralized site in Manila. The existing culture relied heavily on inefficient, non-scalable person-to-person contact.
Redesign Steps:
- Eliminate: Removed redundant questions and answers within the FAQ knowledge base.
- Standardize: Standardized service levels, FAQs, and the overall employee experience globally.
- Optimize: Optimized service loads handled by the helpdesk and refined the FAQ content.
- Automate: Implemented a three-tier support model: a self-service employee portal, webchat support, and direct email/calls reserved for exceptions.
- Robotize: Identified future potential for implementing chatbots to handle common queries.
Key Outcomes: Launched a unified global HR helpdesk (staffed by Capgemini) providing 24/7 support in multiple languages. This resulted in improved efficiency and control (reducing calls/emails), an enhanced employee experience through interactive communication and ownership, and impressively achieved a rapid multinational platform rollout in just five months.
Fortune 500 Engineering/Architecture Company (HR Platform - Billing)
Challenge: A cumbersome, manual timesheet process for contract workers took over four days, involving multiple forms and lengthy paper trails for error correction, delaying billing.
Redesign Steps:
- Eliminate: Got rid of manual forms, reliance on Outlook for communication, physical printouts, and manual signatures.
- Standardize: Created standard forms with common fields for consistency.
- Optimize: Enhanced the ERP system to provide necessary data via API and optimized the RPA interface.
- Automate: Developed a custom digital tool called 'iLabor' for automated timesheet reporting and submission.
- Robotize: Leveraged RPA using API methodology for specific data handling tasks within the process.
Key Outcomes: End-to-end processing time was slashed from over four days to two days. Processing time per request saw a 70% reduction, saving 723 hours annually across the organization. The redesign significantly reduced paper usage, enabled mobile accessibility, generated cost savings, and resulted in faster billing and revenue collection.
Global IT Company (Sales Compensation System)
Challenge: A complex legacy sales compensation system made it difficult and time-consuming for 8,500 sales representatives to track their achievements and access performance data.
Redesign Steps:
- Eliminate: Consolidated over 30 disparate applications into one platform, replaced manual processes with mass uploads, removed manual sales letter workflows, eliminated redundant data/credit processes, and removed multiple tools. 🔗 Read how unifying all your process automation in a single platform can boost control and scalability!
- Standardize: Consolidated regional operational variations into a single global team, standardized manual data feed entry and credit/pay team processes, ensuring consistency globally.
- Optimize: Established a consolidated global team in India implementing best practices, reallocated freed-up resources to drive further improvements, and optimized reporting and database issues.
- Automate: Improved the sales letter process using Macros, automated reconciliation activities, and applied process automation to improve turnaround time, cost, and resource allocation.
- Robotize: Introduced robotics to semi-automate parts of the sales letter generation process.
Key Outcomes: Delivered an integrated platform providing real-time access to sales data for users worldwide. This led to reduced turnaround times, more rapid reporting, enhanced process efficiency, standardization, significant operational cost reduction, faster delivery of compensation letters, and increased data accuracy (e.g., reducing a 12-hour accrual file prep task to 10 minutes and a 4-hour check to 15 minutes).
Digital Supply Chain Redesign Examples
Global Consumer Brands Company (Order-to-Cash)
Challenge: Sought to improve the effectiveness and efficiency of its Order-to-Cash (O2C) processes within the South-East Asia region.
Redesign Steps:
- Eliminate: Removed two entire stages from the order management process flow.
- Standardize: Standardized discounting processes and digitized previously physical documents.
- Optimize: Provided greater visibility into the claims process, leading to a faster claims cycle and optimized the order-to-deliver cycle.
- Automate: Resolved underlying issues in SAP SNC to eliminate manual order creation, enabling automatic generation of "no-touch perfect orders."
- Robotize: Implemented RPA for the end-to-end cash application process, including validations, eliminating physical document handling.
Key Outcomes: Significantly increased the percentage of zero-touch orders and eliminated pricing-related deductions and disputes. A new, replicable target operating model was created. Efficiency gains included a 30% reduction in claims turnaround time and a 20% reduction in overall effort. Effectiveness improved through better controls (no manual interventions), and collections were enhanced using their Webcollect tool. Analytics were leveraged to improve credit control and optimize stock levels.
🎥 Want to boost efficiency and cut waste? Watch our video on the 8 Types of Waste in Lean Management and learn how to streamline your processes!
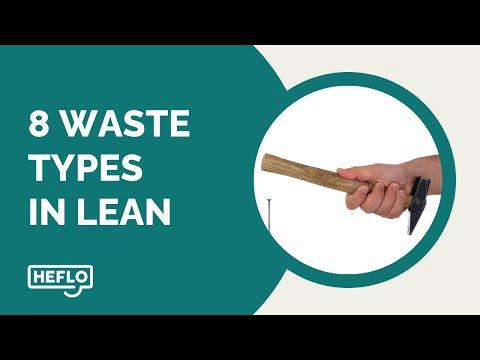
Global Manufacturing Client (Material Requirement Planning)
Challenge: Faced significant process overlaps and duplicated effort in Material Requirement Planning (MRP) between individual factories and a central European hub.
Redesign Steps:
- Eliminate: Removed process overlaps between the hub and factories.
- Standardize: Standardized Order to Deliver processes across all factories.
- Optimize: Optimized the outputs required from factory-level processes.
- Automate: Automated sub-processes related to Purchase Order (PO) generation, reporting, and vendor feedback loops.
- Robotize: Applied RPA to several sub-processes within the MRP workflow.
Key Outcomes: Achieved significant overhead reduction and greater accountability through clarified responsibilities. A governance center was created, and costs were reduced by offshoring some operations. Results included faster PO turnaround, an 85% elimination of PO modifications, a 33% reduction in manual POs, a €24 million reduction in excess inventory, and an over 50% reduction in headcount related to these processes. 50% of activities became rule-based, avoiding transactional decisions.

Financial Services Redesign Example
Global Wealth Management Leader (Data Operations)
Challenge: Dealing with fragmented technology, increasing regulatory pressure, and data quality/governance issues across 20 million securities. Previous piecemeal RPA attempts had failed to deliver significant results.
Redesign Steps:
- Eliminate: Removed manual interface monitoring, manual index updates, concurrent audits of manual setups/amendments, temporary amendments (once automated), and manual watermarking of documents.
- Standardize: Standardized manual data entry for instrument setups/amendments, standardized templates (setup, pricing), and standardized the request intake channel.
- Optimize: Optimized request templates, reporting rules, trace functions for instrument creation, and the knowledge base for query resolution.
- Automate: Automated setups for various instrument types (non-term sheets, bonds, EQ), automated temporary amendment processing/reversal, automated report generation, and automated priority/agent assignment.
- Robotize: Used RPA for end-of-day pricing (improving accuracy/turnaround) and license cost monitoring/reduction.
Key Outcomes: Identified significant savings potential (30–40% cost efficiency improvement) and a potential reduction of over 50 FTEs. The redesign reduced process risk, improved data quality, and enhanced risk reduction and regulatory compliance. Crucially, it highlighted the need for cultural change alongside technological transformation, initiating an augmented workforce initiative.
📘 Want more consistency and efficiency? Read our article on Process Standardization and learn how to simplify operations across your organization!
Insurance Redesign Example
US Supplemental Health Insurance Company (Claims Processing)
Challenge: Faced scalability issues due to growing claims volumes submitted through diverse channels (fax, email, mail), hindering their 24-hour response promise. Digitization was needed as a foundation for automation.
Redesign Steps:
- Eliminate: Removed unnecessary fields from the claims submission process and eliminated associated redundant internal tasks.
- Standardize: Developed a single, standardized claims form, extracting only relevant client-specific data from 45 potential fields.
- Optimize: Simplified, streamlined, and optimized the end-to-end claims processing flow while maintaining claimant flexibility.
- Automate: Implemented automated data extraction and processing for submitted claims.
- Robotize: Reserved human intervention primarily for handling exceptions identified by the automated system.
Key Outcomes: The redesign enhanced operational efficiency, improved the customer experience, increased quality and compliance adherence, and enhanced overall business agility. It effectively created a "data-extraction-as-a-service" operation, setting the stage for future intelligent bot implementation to further automate the process.
🧩 See a real-world example of a Customer Service process in action—learn how to deliver faster, more reliable support!
Key Learnings from Business Process Redesign Case Studies
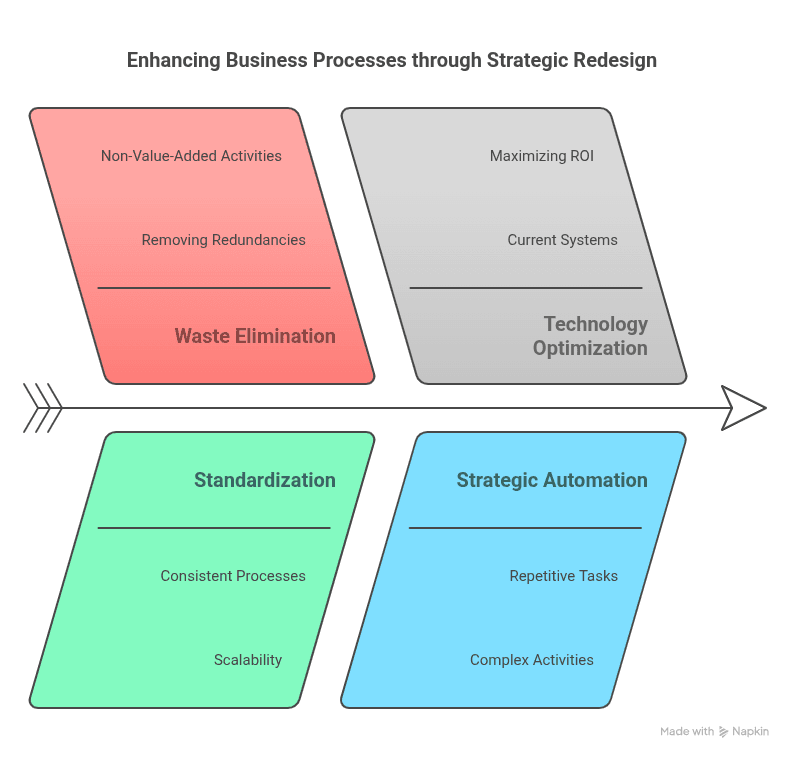
These diverse business process redesign examples consistently highlight several key learnings:
- Focus on Eliminating Waste First: Significant gains in efficiency and cost reduction often come from simply removing unnecessary steps, redundancies, and non-value-added activities before applying technology.
- Standardization is Crucial: Creating consistent, "golden path" processes is essential for scalability, control, and effective automation. Automating inconsistent or highly variable processes is difficult and often ineffective.
- Optimize Existing Tech: Don't overlook the potential of your current systems. Optimizing ERPs, workflows, and other existing tools can provide quick wins and maximize ROI on previous investments.
- Strategic Automation/Robotization: Automation and RPA deliver the best results when applied thoughtfully to standardized, optimized processes, targeting repetitive, rule-based tasks and freeing up human workers for more complex activities.
- Quantifiable Results Matter: The value of BPR is best demonstrated through measurable improvements in metrics like time saved (e.g., days to minutes), cost reduction (€ millions, FTE reduction), efficiency gains (%), error reduction, and improved compliance or satisfaction scores.
- Broad Applicability: BPR and methodologies like ESOAR are not limited to one function or industry; they can drive transformative results in finance, HR, supply chain, customer service, insurance, manufacturing, retail, and more.
Starting Your Own Business Process Redesign Initiative
Inspired by these examples? Embarking on your own BPR journey involves a structured approach:
- Identify Bottlenecks and Pain Points: Start by pinpointing processes that are slow, costly, error-prone, or frustrating for customers or employees. Use data, surveys, and interviews.
- Define Clear Goals and Metrics: What does success look like? Set specific, measurable, achievable, relevant, and time-bound (SMART) goals for improvement (e.g., reduce processing time by 50%, cut costs by 15%).
- Choose a Suitable Methodology: Select a framework like ESOAR, Lean, Six Sigma, or others to guide your redesign efforts.
- Map Current vs. Desired Future State: Document the existing ("as-is") process in detail. Then, design the radically improved ("to-be") process, incorporating elimination, standardization, and optimization principles.
- Implement Changes Iteratively: Roll out changes in manageable phases, starting with pilot programs where feasible. Manage change effectively through clear communication, training, and stakeholder involvement.
- Measure Results and Continuously Improve: Track performance against your defined metrics. Analyze the results, gather feedback, and make further adjustments as needed. BPR is often an ongoing cycle of improvement.
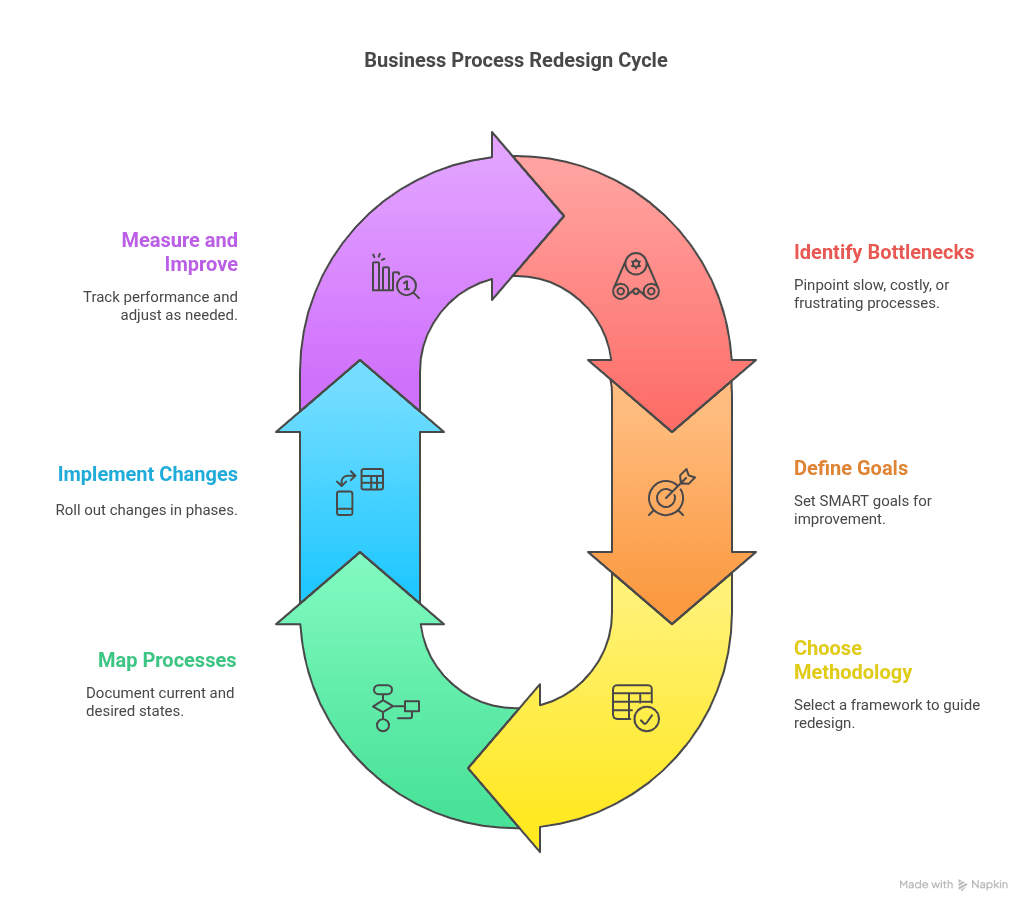
Conclusion: Unlock Potential with Strategic Business Process Redesign
As demonstrated by these real-world business process redesign examples, strategically rethinking and redesigning core operations unlocks significant potential. Applying methodologies like ESOAR drives dramatic improvements in efficiency, substantial cost savings, enhanced quality, and better experiences for both customers and employees across diverse business functions. Evaluate your internal processes today for redesign opportunities.
📄 Want to dive deeper? Access the original ESOAR PDF on Capgemini’s official website for the complete methodology and real success stories!
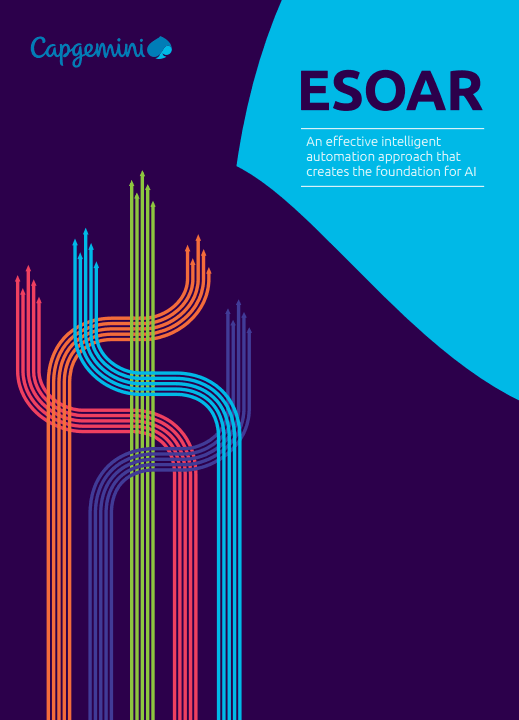