Business Process Mapping: Understanding and Improving Workflows
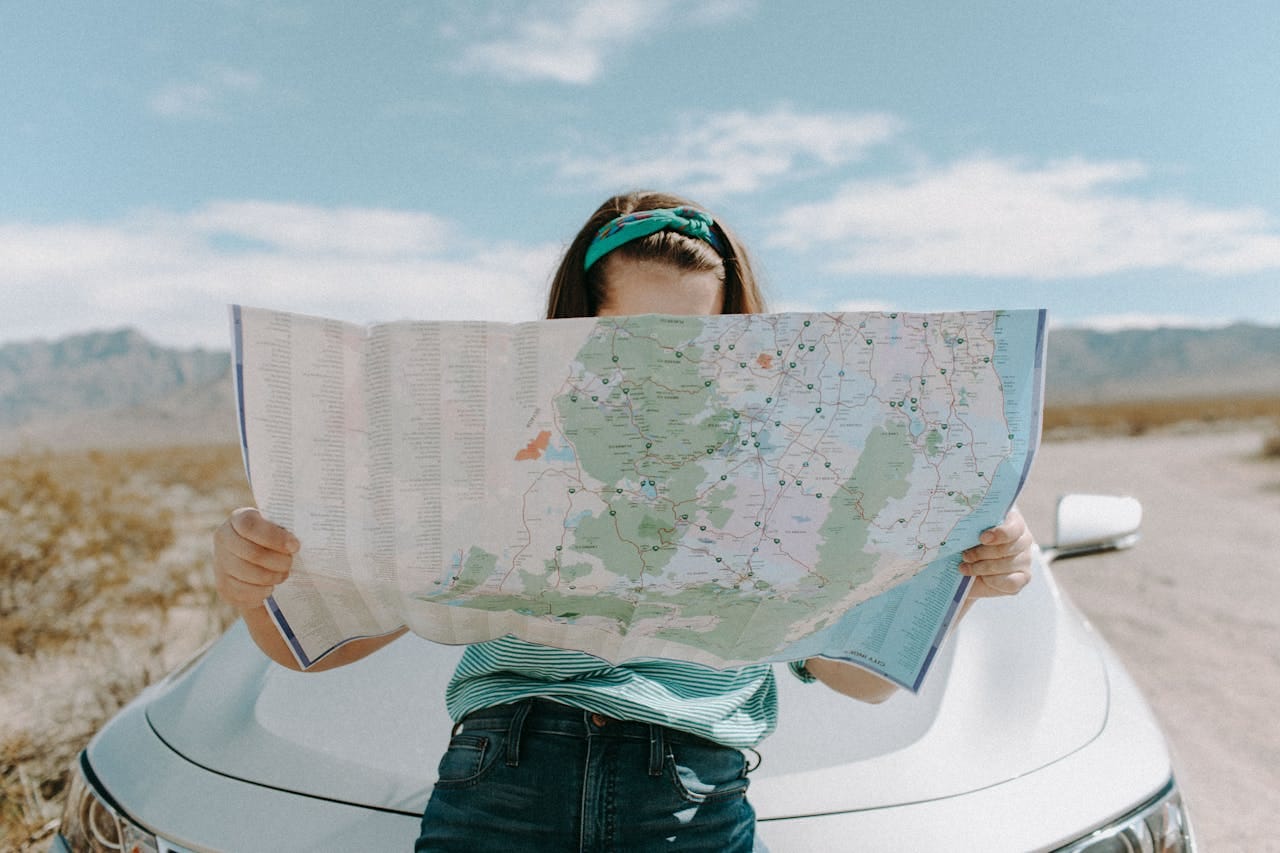
Business process mapping empowers organizations to rethink how work gets done. By transforming everyday tasks into visual journeys, teams can uncover hidden inefficiencies, spark innovation, and align efforts toward achieving greater operational success.
π₯ Watch: What Is Business Process Mapping and Why It Matters
This short video explains the purpose, benefits, and common mistakes of process mapping β and gives you a clear step-by-step approach to start your own.
Ideal if you're new to the topic or want a quick, expert summary.
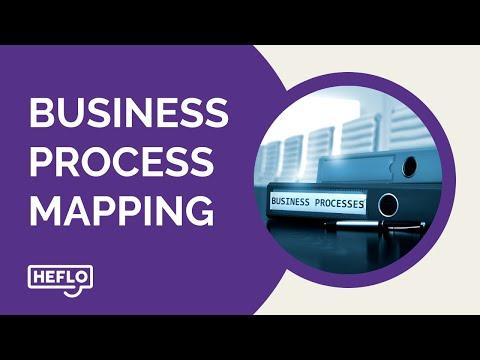
What Is Business Process Mapping?
Business process mapping is the act of visually documenting the steps, roles, inputs, and outputs involved in a business process. The goal is to provide a clear understanding of how tasks are performed, who is responsible, and what tools or systems are used along the way.
These maps often take the form of flowcharts, swimlane diagrams, or BPMN (Business Process Model and Notation) diagrams.
Benefits of Business Process Mapping
Business process mapping goes far beyond drawing flowcharts β it reveals how your organization truly works beneath the surface. By making workflows visual and easy to grasp, teams gain clarity, leaders make smarter decisions, and hidden inefficiencies are brought to light.
The impact spans every department: aligning teams, speeding up operations, and fueling a culture of continuous improvement. It's not just a tool β itβs a catalyst for transformation.
π Curious What This Looks Like in Action?
Let the visual below show you.
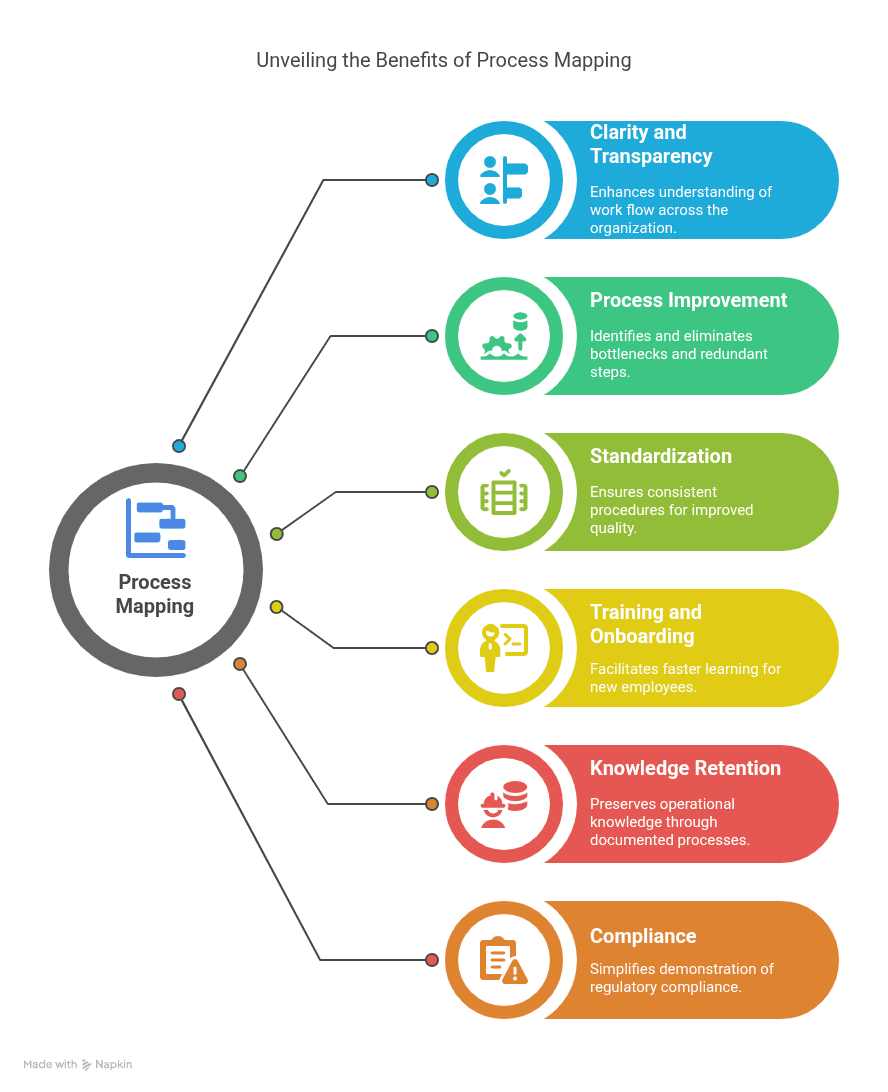
How to Create a Business Process Map
Creating an effective business process map involves more than just outlining tasks β it requires collaboration, analysis, and refinement. Hereβs a step-by-step guide:
Step 1 - Choose the process to map
Not all processes should be mapped at once β itβs important to start with those that offer the highest potential value. To prioritize, you can use the following techniques:
- Identify high-impact processes:
Focus on processes that directly influence business outcomes, such as:- Customer-facing processes
- Revenue-generating workflows
- Activities that support other high-value or core business functions
- Cross-functional processes critical for coordination
- Use a scoring model:
Assign scores to processes based on key factors like business impact, frequency, risk, and strategic alignment. This helps objectively determine which processes should be mapped first. - Align with organizational goals:
Ensure selected processes directly support strategic priorities and critical business outcomes. Mapping should not be done in isolation β it must contribute to real improvements aligned with business objectives.
Step 2 - Identify stakeholders and gather information
Interview those directly involved in the execution or management of the process. In addition to conversations, collect documentation that reflects the current state of the process. This helps ensure that the mapping is grounded in reality, not assumptions. Useful sources include:
- Standard Operating Procedures (SOPs)
- Internal policies and compliance manuals
- Forms, checklists, and templates
- Audit reports and performance indicators
- Screenshots of systems and software used
- Training materials and onboarding content
- Previous diagrams or workflow notes
- Emails or tickets describing issues or exceptions
Use custom spreadsheets to collect step-by-step information from process participants. These templates can include columns for task names, responsible roles, input/output, duration, and tools used.
Step 3 - List the steps in order
After collecting all relevant data, the analyst must carefully analyze and compile the information to identify the core processes and their respective tasks. This includes organizing the inputs gathered from interviews, documents, and worksheets into a structured sequence of activities that reflect how the process truly operates. The goal is to build a clear, logical flow of work that represents the current or ideal state of the process.
Step 4 - Draw the process map using software tools
In addition to creating a visual diagram, it is equally important to provide detailed textual documentation that explains each step, decision point, and role involved in the process. This ensures full understanding and supports training, audits, and continuous improvement.
HEFLO stands out in this area by allowing you to complement BPMN diagrams with rich, embedded textual descriptions directly in the same interface β a key advantage over traditional tools.Use diagramming tools like HEFLO, Lucidchart, or Visio to create your map.
π Want help with BPMN? Read our guide on how to design a BPMN process flow.
Step 5 - Review and validate the map with your team
Ensure the process map accurately reflects how the work is performed. This validation should include not only the team involved in the mapping effort, but also the process owner and key stakeholders who participate in or are impacted by the process. Their involvement is essential to confirm that the representation aligns with real-world operations, to resolve any misunderstandings, and to ensure shared understanding and accountability.
Step 6 - Communicate and share the process
Once the process map is validated, it should be made accessible to all relevant stakeholders. This can be done by publishing the process in a dedicated process portal, allowing employees to interact with and navigate the map online.
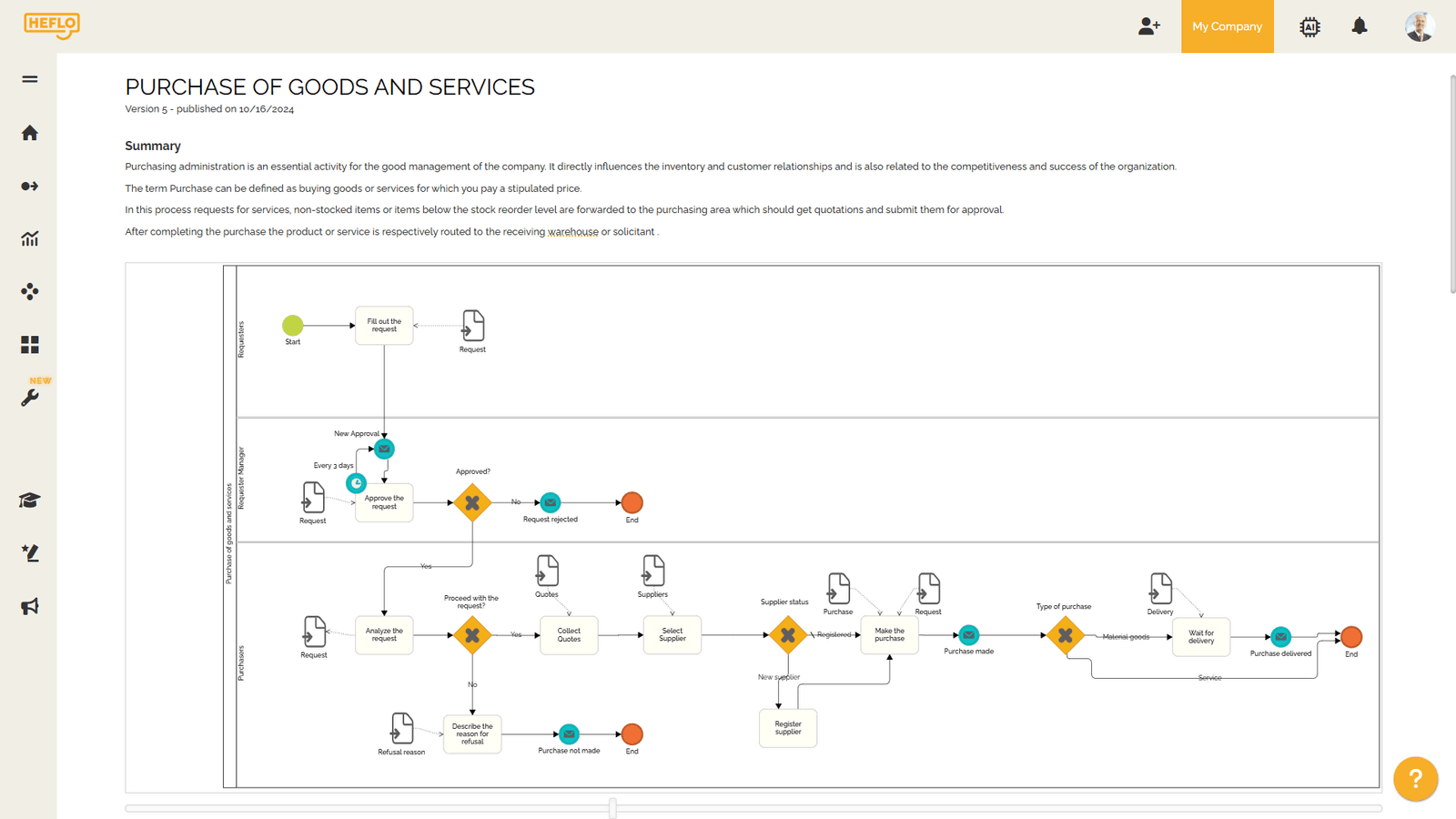
Alternatively, you can export the documentation to PDF and share it via email, intranet, or document management systems.
π Download a sample PDF with a documented process to see what a final deliverable can look like.
Step 7 - Update the map as the process evolves
Treat it as a living document β refine it as business needs change. To ensure lasting value, continuous improvement should be integrated into the lifecycle of every mapped process. One effective approach is to establish a process governance or improvement management workflow that collects, evaluates, and implements suggestions for enhancement.
Access a ready-to-use improvement management process flow here.
β Your Step-by-Step Guide: The Complete Business Process Mapping Checklist
Before jumping into flowcharts and diagrams, it's crucial to approach process mapping with structure and clarity. This comprehensive checklist walks you through every stage β from preparation and stakeholder engagement to process validation and continuous improvement.
1. Planning and Preparation
- Define the purpose of the mapping (e.g., automation, documentation, redesign)
- Select a process that is critical or frequently used
- Identify the scope: where the process begins and ends
- Confirm executive sponsorship (if required)
- Identify the expected outcomes or success criteria
- Choose the right mapping method (e.g., flowchart, swimlane, BPMN)
- Select a tool or platform for visualization (e.g., HEFLO, Lucidchart, Visio)
2. Stakeholder Engagement
- Identify all individuals and teams involved in the process
- Schedule interviews or workshops to capture current steps
- Ensure involvement of frontline users (not just managers)
- Set expectations for collaboration and review
3. Mapping the Current Process (As-Is)
- List all major steps in logical order
- Identify decisions, approvals, and exceptions
- Include who performs each step (roles, not individual names)
- Highlight any tools, documents, or systems involved
- Use clear, simple language in descriptions
- Identify handoffs or points where delays tend to occur
4. Validation and Feedback
- Review the draft process map with stakeholders
- Confirm accuracy of each step and decision
- Clarify any ambiguous or redundant activities
- Revise the map based on feedback
5. Analysis and Improvement (To-Be Design)
- Identify bottlenecks, delays, or duplication
- Highlight steps that could be automated or eliminated
- Evaluate alignment with strategic goals
- Prioritize improvements with the greatest impact
- Design the improved βto-beβ process (if applicable)
- Assess risks or dependencies before implementation
6. Communication and Implementation
- Share updated maps with all relevant stakeholders
- Provide training if the new process changes responsibilities
- Ensure version control and access to the most current map
- Document any changes formally (e.g., in a process repository)
7. Monitoring and Continuous Improvement
- Define KPIs or success metrics to track performance
- Set review frequency (e.g., quarterly, annually)
- Assign process owner responsible for ongoing updates
- Establish a feedback loop for future improvements
Prefer the MS Excel version? click here to download it.
β No email. No forms. Just the file.
As-Is vs. To-Be Process Mapping
When mapping business processes, itβs important to understand the distinction between As-Is and To-Be process mapping. These two approaches serve different but complementary purposes in the context of process analysis and improvement.
- As-Is process mapping represents the current state of a process β how it actually operates today, including all existing steps, roles, tools, and bottlenecks. This view is essential for identifying inefficiencies, redundancies, and deviations from standards.
- To-Be process mapping defines the desired future state of the process β how it should function after improvements are made. It reflects optimized workflows, automation opportunities, and redesigned steps aligned with business goals.
Hereβs a quick side-by-side comparison to reinforce the key distinctions between βas isβ and βto beβ process mapping.
π Aspect | π°οΈ "As Is" Process Mapping | π "To Be" Process Mapping |
---|---|---|
Purpose | Document the current process | Envision the improved future-state process |
Focus | What exists today, including inefficiencies | What should exist after improvements |
Approach | Observational and diagnostic | Design-oriented and goal-driven |
Typical Use Cases | Audits, compliance, training, root-cause analysis | Process redesign, automation planning, digital transformation |
Outputs | Current flowcharts, exception paths | Optimized process diagrams, clear handoffs, KPIs |
Risks if Skipped | You may not identify all current issues | You may automate flawed or unnecessary steps |
π Want real-world inspiration? Explore business process redesign examples by Capgemini in this article.
Process Governance and Ownership
A well-mapped process without governance is like a blueprint no one follows. To drive real results, organizations must define who owns each process and how it will be maintained over time.
Without clear governance, process maps quickly become outdated and disconnected from daily operationsβlosing their power as tools for decision-making, training, and improvement.
A solid governance framework ensures accountability, keeps teams aligned, and reinforces the link between operations and strategic goals.
Key Elements of Process Governance
- Process Ownership
Every process should have a clearly defined owner β someone accountable for its accuracy, performance, and evolution. This role is typically assigned to a business manager or operational lead directly involved with the process. - Review and Update Cycles
Governance includes setting regular review intervals (e.g., every 6 or 12 months) to update the process based on changes in tools, policies, or business models. - Change Management and Version Control
Formal procedures should exist to manage updates, with approval workflows and documentation of changes to maintain process integrity and compliance. - Process Repository and Accessibility
All approved process maps should be published in a centralized, easily accessible process portal, ensuring visibility for stakeholders and new team members. - Integration with Continuous Improvement
Governance frameworks should be linked to suggestion workflows, enabling employees to propose enhancements and trigger analysis cycles led by the process owner.
β Frequently Asked Questions
1. What is the first step in analyzing a business process?
The first step is to identify and define the process. This includes understanding its purpose, setting clear boundaries, and determining key stakeholders involved. This foundation ensures that the analysis remains focused and relevant.
2. How do you gather information for process mapping?
You can gather information through:
- Interviews with people involved in the process
- Observation of actual workflows
- Reviewing documents and SOPs
- Workshops or collaborative sessions with stakeholders
Combining multiple sources helps capture both the documented and informal aspects of the process.
3. What are the information requirements for a process map?
To create a meaningful process map, you need:
- Process steps and sequence
- Roles and responsibilities
- Inputs and outputs
- Decisions and exceptions
- Relevant documents or tools
- Start and end points of the process
4. What is included in a process map?
A process map typically includes:
- Activities/tasks
- Events (start/end)
- Decision points
- Flows or transitions
- Swimlanes (to show who does what)
- Inputs and outputs for each step
5. What are the requirements for a mapping tool?
A good process mapping tool should offer:
- Support for standard notations (e.g., BPMN)
- Drag-and-drop interface
- Collaboration features
- Version control and change tracking
- Export options (PDF, PNG, XML)
- Integration with other business tools
6. What are the key points of process mapping?
Key points include:
- Clarity: Make the process easy to understand.
- Accuracy: Reflect the real process, not just the ideal.
- Completeness: Include all steps, roles, and decisions.
- Consistency: Use a standardized format or notation.
- Improvement-oriented: Identify inefficiencies or risks.
7. What questions to ask when mapping a process?
Ask questions such as:
- What triggers the process to start?
- What are the key steps involved?
- Who is responsible for each step?
- What tools or documents are used?
- Where do delays or errors typically occur?
- What is the desired outcome?
8. Is a process map an SOP?
Not exactly. A Standard Operating Procedure (SOP) is a detailed written document describing how to perform tasks. A process map is a visual representation of the workflow. They are often used together β the map provides the overview, while the SOP provides the instructions.
9. What are the three main categories of process maps?
The three common types are:
- High-level process maps (overview or value chain)
- Detailed process maps (step-by-step with decisions)
- BPMN diagrams (showing responsibilities across roles or departments)
10. How to do process mapping if you have zero domain knowledge?
If you're unfamiliar with the domain:
- Start by interviewing subject matter experts
- Observe the process in action
- Request documentation or SOPs
- Create an initial draft and validate it iteratively with stakeholders
- Use simple visual tools and ask clarifying questions often
π Learn by example β read our article βA Simple and Straightforward Process Mapping Exampleβ for a clear, practical walkthrough.11. How can I improve my process mapping skills?
You can improve by:
- Studying BPMN or Lean Six Sigma techniques
- Practicing with real or simulated processes
- Using tools like Lucidchart, HEFLO, or Bizagi
- Reviewing case studies and existing maps
- Getting feedback from process experts
12. What is the difference between a process map and a flowchart?
A flowchart is a basic diagram showing the flow of steps in a process, often without roles or context. A process map, especially in BPMN, includes roles, events, documents, decisions, and interactions, making it more comprehensive and business-focused.
13. Is a workflow the same as a process map?
Not quite. A workflow is the actual sequence of tasks and activities performed to complete a process. A process map is the visual model or diagram of that workflow. The map helps analyze and optimize the workflow.
π Recommended Books on Business Process Mapping
From foundational concepts to advanced techniques, these books deliver practical and strategic guidance on process modeling, BPMN standards, and digital innovation.
1. BPMN Method and Style β Bruce Silver
The definitive guide to BPMN 2.0 β ideal for anyone who wants to model processes clearly and correctly, following best practices and professional standards.
ποΈ Buy on Amazon
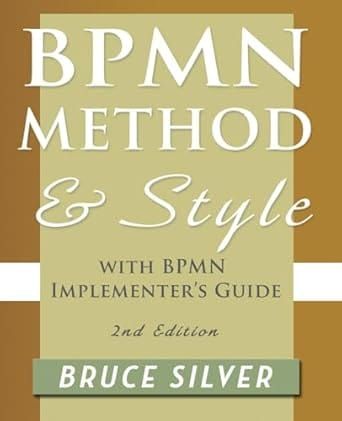
2. Business Process Change β Paul Harmon
A foundational book on business process redesign, digital transformation, and how organizations evolve using process thinking.
ποΈ Buy on Amazon
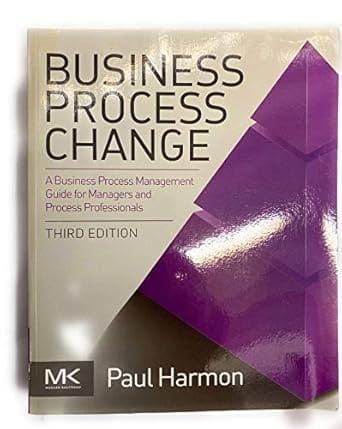
3. Improving Business Processes β Harvard Business Review Press
A concise, practical introduction to process improvement with real business examples. Accessible and action-oriented.
ποΈ Buy on Amazon
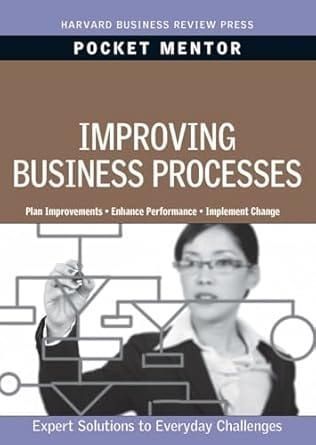
4. Real-Life BPMN β Jakob Freund & Bernd RΓΌcker
A modern, visual take on BPMN β focused on agile teams, digital platforms, and practical use with workflow automation tools.
ποΈ Buy on Amazon
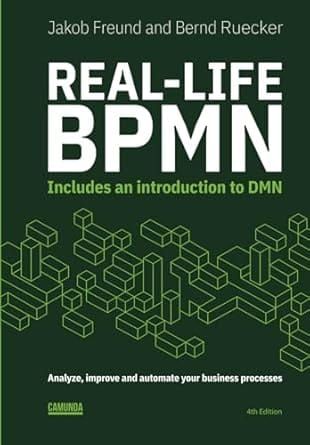
Conclusion: Turning Insights into Action
Business process mapping is more than just a documentation exercise β it's a strategic tool to drive efficiency, foster collaboration, and prepare your organization for digital transformation. By understanding how work really gets done, you lay the groundwork for smarter systems and better outcomes.
π Ready to put process mapping into practice?
Explore our free BPMN templates or open a sample process directly in the HEFLO BPMN editor to start mapping your own workflows today.
π Want to go further?
Check out our guides on Business Process Automation and Organizational Process Documentation to continue your journey toward operational excellence.