Desatando el Poder de Lean Six Sigma DMAIC: Una Guía Paso a Paso para la Mejora de Procesos
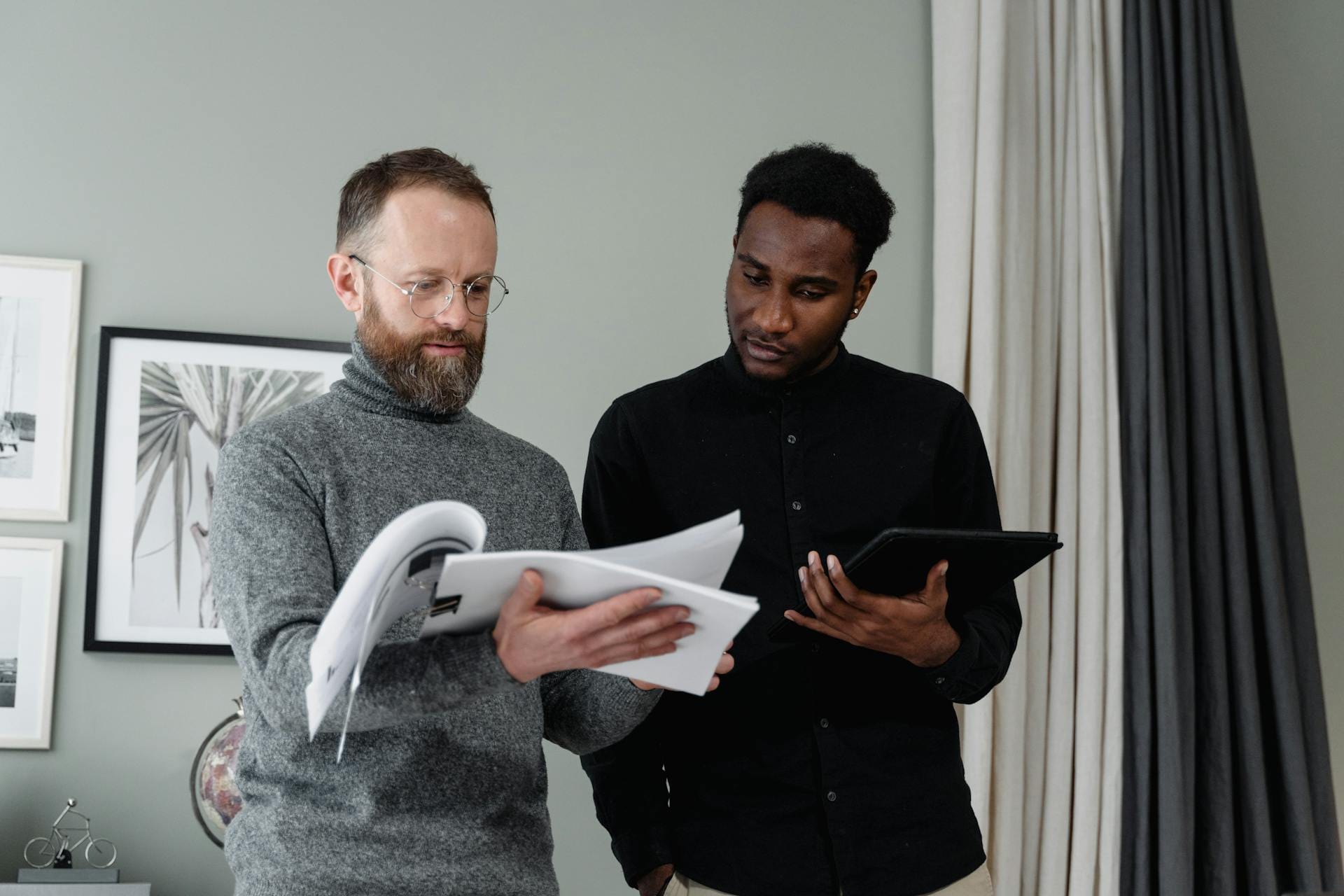
Desbloquea el potencial de Lean Six Sigma DMAIC con nuestra guía completa paso a paso para la mejora de procesos. Este artículo profundiza en cada fase crítica: Definir, Medir, Analizar, Mejorar y Controlar. Los lectores pueden esperar una exploración detallada de metodologías y consejos prácticos para mejorar la eficiencia y la calidad en sus procesos. Ya sea que seas nuevo en Lean Six Sigma o busques perfeccionar tus habilidades, esta guía ofrece valiosas ideas para impulsar cambios impactantes en tu organización.
Fase de Definición
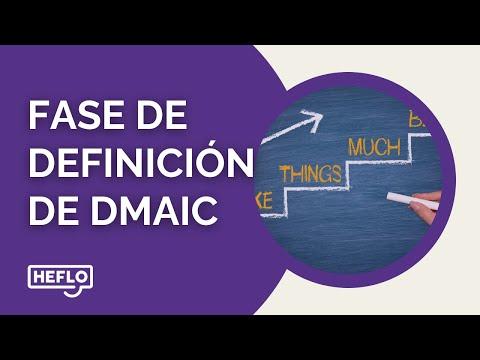
La Fase de Definición es el primer paso en la metodología DMAIC (Definir, Medir, Analizar, Mejorar, Controlar) de Lean Six Sigma. Esta fase establece la base para todo el proyecto de mejora de procesos al identificar claramente el problema, establecer objetivos y definir el alcance del proyecto.
Durante la Fase de Definición, es esencial crear un acta del proyecto que describa la declaración del problema, los objetivos del proyecto y los indicadores clave de rendimiento (KPIs). Este documento sirve como un acuerdo formal entre las partes interesadas y proporciona una dirección clara para el equipo del proyecto. Además, el acta del proyecto ayuda a asegurar los recursos y el apoyo necesarios de la alta dirección.
Otra actividad crítica en esta fase es identificar la Voz del Cliente (VoC). Comprender las necesidades y expectativas del cliente es vital para asegurar que las mejoras del proceso se alineen con los requisitos del cliente. Se pueden emplear técnicas como encuestas, entrevistas y grupos focales para recopilar esta información.
El mapeo de procesos también es un componente significativo de la Fase de Definición. Crear un mapa de alto nivel del proceso actual ayuda a visualizar el flujo de trabajo e identificar áreas clave para la mejora. Herramientas como los diagramas SIPOC (Proveedores, Entradas, Proceso, Salidas, Clientes) se utilizan a menudo para proporcionar una visión integral del proceso.
Para las empresas que buscan documentar y automatizar sus procesos de negocio, herramientas como HEFLO pueden ser invaluables. HEFLO ofrece una plataforma basada en la nube que simplifica la creación de mapas de procesos y asegura que todas las partes interesadas tengan acceso a la documentación actualizada del proceso.
Mira nuestro último video sobre la documentación de procesos de negocio y descubre cómo transformar tu organización para lograr la máxima eficiencia. ¡No te lo pierdas, tu camino hacia un mejor negocio comienza aquí!
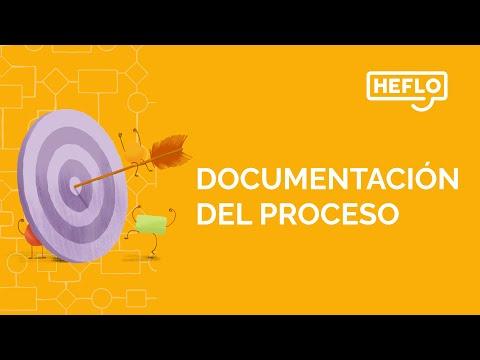
Finalmente, es crucial establecer un equipo de proyecto con roles y responsabilidades claramente definidos. El equipo debe incluir expertos en la materia, propietarios del proceso y otras partes interesadas clave que puedan aportar conocimientos valiosos e impulsar el proyecto hacia adelante. La comunicación y colaboración efectivas entre los miembros del equipo son esenciales para el éxito de la Fase de Definición.
Fase de Medición
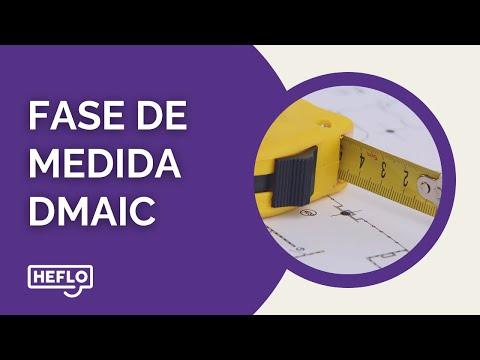
En la metodología DMAIC de Lean Six Sigma, la fase de Medición es donde se establece la base para la toma de decisiones basada en datos. Esta fase se centra en cuantificar el rendimiento actual del proceso para identificar áreas de mejora. La medición precisa es esencial para comprender las capacidades del proceso existente y establecer una línea base para futuras mejoras.
Sin datos, solo eres otra persona con una opinión. - W. Edwards Deming
Durante la fase de Medición, se recopilan varios métricos para proporcionar una visión integral del rendimiento del proceso. Estos métricos a menudo incluyen:
- Puntualidad: Métricos como el rendimiento, el tiempo de ciclo y las fechas de entrega ayudan a comprender la eficiencia del proceso.
- Calidad del Producto: Métricos como las tasas de defectos, el volumen de retrabajo y la fiabilidad del producto son cruciales para evaluar la calidad del resultado.
- Calidad del Servicio: Los métricos de capacidad de respuesta, confiabilidad y fiabilidad del servicio proporcionan información sobre la experiencia del cliente.
- Costo: El costo de la mano de obra, el costo de los materiales, los gastos generales y el costo del retrabajo se miden para evaluar el impacto financiero del proceso.
- Satisfacción del Cliente: Métricos que evalúan si el producto o servicio cumple con las expectativas del cliente.
La recopilación de datos precisos es crítica en esta fase. Implica el uso de herramientas como el Mapeo de la Cadena de Valor, la Contabilidad Basada en Actividades y el Control Estadístico de Procesos para monitorear y controlar los procesos. Estas herramientas ayudan a visualizar la cadena de valor, comprender los impulsores de costos y mantener el control estadístico sobre el proceso.
La medición del rendimiento no se trata solo de recopilar datos; se trata de garantizar que los datos sean precisos, completos, consistentes y oportunos. Esta fase a menudo implica la configuración de paneles de control en tiempo real y sistemas de medición del rendimiento para proporcionar información continua sobre el rendimiento del proceso. Al integrar la medición del rendimiento en las operaciones diarias, las empresas pueden identificar rápidamente problemas e implementar cambios para optimizar sus procesos.
Para las empresas que buscan documentar y automatizar sus procesos de negocio, herramientas como HEFLO pueden ser invaluables en la fase de Medición de Lean Six Sigma DMAIC.
Fase de Análisis
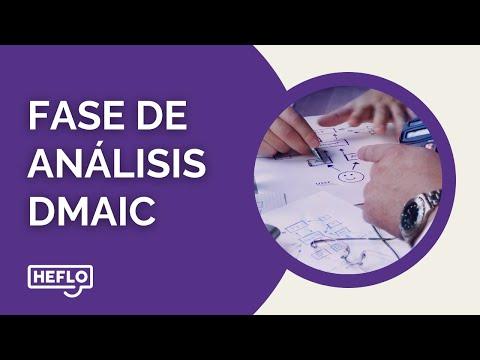
En la fase de Análisis de la metodología DMAIC, el objetivo principal es identificar las causas raíz de las ineficiencias y defectos del proceso. Esta fase implica un examen exhaustivo de los datos recopilados durante la fase de Medición para descubrir patrones, correlaciones y conocimientos que puedan informar las estrategias de mejora.
Uno de los primeros pasos en la fase de Análisis es elegir los marcos analíticos y metodologías apropiados. No existe un enfoque único para todos; la elección depende de la naturaleza del proceso y los datos disponibles. Métodos formales como Six Sigma y Lean proporcionan una variedad de herramientas y plantillas que pueden ser extremadamente útiles. Por ejemplo, herramientas como los diagramas de causa y efecto, los gráficos de Pareto y el análisis de regresión se emplean comúnmente para identificar áreas problemáticas.
A menudo es necesario descomponer procesos más grandes en subprocesos más pequeños y manejables. Esto no solo ayuda a gestionar la complejidad, sino también a mostrar el progreso a las partes interesadas. El equipo de análisis debe ser cauteloso con la "parálisis por análisis", donde el exceso de análisis puede llevar a retrasos y pérdida de interés entre los miembros del equipo. Para evitar esto, el alcance del análisis debe mantenerse pequeño y enfocado, asegurando que el progreso sea visible y continuo.
Las entrevistas con individuos de varias funciones de negocio pueden proporcionar conocimientos valiosos y ayudar a tomar decisiones informadas sobre el alcance. Cuantas más funciones y actividades de negocio se incluyan en el análisis, más complejo y prolongado se vuelve. Por lo tanto, es crucial equilibrar la profundidad del análisis con la necesidad de resultados oportunos.
La documentación es un componente clave de la fase de Análisis. Esto incluye una visión general del entorno de negocio actual, el propósito del proceso, un modelo de proceso detallado y la identificación de brechas de rendimiento. Además, la documentación debe resaltar redundancias que pueden ser eliminadas y proporcionar soluciones recomendadas. Esto sirve como un acuerdo formal sobre la precisión del análisis y forma la base para presentar resultados a la gerencia.
Las reuniones diarias del equipo pueden ser beneficiosas para discutir hallazgos y reconocer patrones. Este enfoque colaborativo asegura que todos los miembros del equipo estén alineados y puedan contribuir a identificar oportunidades de mejora. El análisis también debe centrarse en los entregables de la unidad de negocio o subproceso, asegurando que todo el trabajo contribuya a estos entregables.
Fase de Mejora
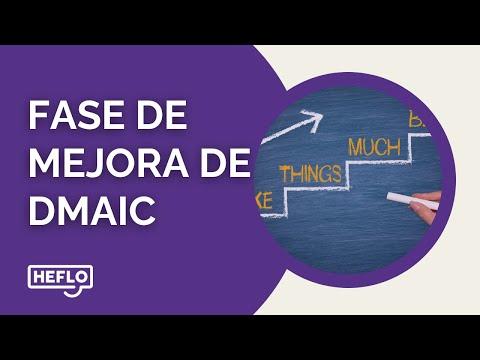
La fase de Mejora de la metodología DMAIC (Definir, Medir, Analizar, Mejorar, Controlar) es donde tiene lugar la transformación real de los procesos. Esta fase se centra en identificar, probar e implementar soluciones a los problemas identificados en las fases anteriores. El objetivo es optimizar los procesos para lograr un mejor rendimiento, calidad y eficiencia.
Durante la fase de Mejora, los equipos generan ideas para posibles soluciones y utilizan diversas herramientas y técnicas para identificar las mejoras más efectivas. Técnicas como sesiones de lluvia de ideas, análisis de causa raíz y análisis de modos de falla y efectos (FMEA) son comúnmente empleadas. Estas herramientas ayudan a generar una amplia gama de ideas y a evaluar su impacto potencial en el proceso.
Una vez identificadas las posibles soluciones, se prueban a través de ejecuciones piloto o simulaciones. Este paso es crucial para asegurar que los cambios propuestos conduzcan a las mejoras deseadas sin causar consecuencias no deseadas. Los datos recopilados durante estas pruebas se analizan para verificar la efectividad de las soluciones. A menudo se utilizan herramientas estadísticas y gráficos de control para comparar el rendimiento del proceso antes y después de la implementación de las mejoras.
Además de probar soluciones, la fase de Mejora también implica refinar y optimizar el proceso. Esto puede incluir minimizar las transferencias, asegurarse de que cada acción agregue valor al proceso y gestionar los datos o insumos del producto cerca de la fuente. El equipo revisa el proceso para asegurarse de que todos los participantes ejecuten con precisión la misma mejor práctica, impulsando la eficiencia y efectividad del proceso.
Finalmente, el equipo diseña controles y guías del proceso para asegurar la ejecución consistente del proceso mejorado. Este paso es esencial para reducir o eliminar variaciones, excepciones y errores. Al estandarizar el proceso mejorado, las organizaciones pueden lograr mejoras sostenibles y mantener altos niveles de rendimiento a lo largo del tiempo.
Fase de Control
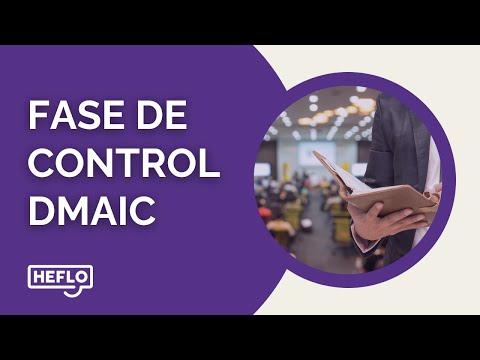
En la metodología DMAIC de Lean Six Sigma, la Fase de Control se dedica a mantener las mejoras logradas durante las fases anteriores. Esta fase asegura que los cambios en el proceso se sostengan en el tiempo y que las ganancias no se pierdan. Involucra la implementación de mecanismos de control y sistemas de monitoreo para mantener el proceso dentro de los niveles de rendimiento deseados.
Actividades Clave en la Fase de Control
Se llevan a cabo varias actividades críticas durante la Fase de Control para asegurar la estabilidad y sostenibilidad del proceso mejorado:
- Desarrollar Planes de Control: Se crea un plan de control para documentar los métodos y métricas que se utilizarán para monitorear el proceso. Este plan incluye detalles sobre qué se necesita medir, con qué frecuencia deben tomarse las mediciones y quién es responsable del monitoreo.
- Implementar Sistemas de Monitoreo: Se utilizan herramientas como gráficos de Control Estadístico de Procesos (SPC) para rastrear el rendimiento del proceso. Estos gráficos ayudan a identificar cualquier variación que pueda indicar una desviación del rendimiento deseado del proceso.
- Estandarizar Procedimientos: Se actualizan o crean procedimientos operativos estándar (SOP) para reflejar las nuevas mejoras del proceso. Esto asegura que todos los miembros del equipo sigan las mismas mejores prácticas, reduciendo la variabilidad y manteniendo la consistencia.
- Capacitación y Documentación: Se llevan a cabo programas de capacitación para educar a los empleados sobre los nuevos cambios en el proceso y los mecanismos de control. También se mantiene una documentación completa para proporcionar una referencia para futuras auditorías y revisiones del proceso.
- Establecer Planes de Respuesta: Se desarrollan planes de respuesta para abordar cualquier problema que pueda surgir. Estos planes delinean los pasos a seguir si el proceso se desvía de los límites de control, asegurando acciones correctivas rápidas y efectivas.
Métricas de Rendimiento
Las métricas de rendimiento juegan un papel crucial en la Fase de Control. Estas métricas ayudan a evaluar si el proceso está funcionando como se espera y cumpliendo con los objetivos establecidos. Las métricas de rendimiento comunes incluyen:
- Puntualidad: Medidas como el rendimiento, el tiempo de ciclo y las fechas de entrega.
- Calidad del Producto: Métricas como tasas de defectos, volumen de retrabajo y fiabilidad del producto.
- Calidad del Servicio: Indicadores como capacidad de respuesta, confiabilidad y fiabilidad del servicio.
- Costo: Incluye costo de mano de obra, costo de materiales, gastos generales y costo de retrabajo.
- Satisfacción del Cliente: Evalúa si el producto o servicio cumple con las expectativas del cliente.
Mejora Continua
La Fase de Control no se trata solo de mantener el statu quo; también implica la mejora continua. Al revisar regularmente los datos de rendimiento y la retroalimentación, las organizaciones pueden identificar nuevas oportunidades de mejora y asegurar que el proceso evolucione para satisfacer las necesidades y condiciones cambiantes.
En conclusión, desatar el poder de Lean Six Sigma DMAIC ofrece un enfoque estructurado y efectivo para la mejora de procesos que puede impulsar mejoras significativas en calidad, eficiencia y satisfacción del cliente. Al seguir meticulosamente las fases de Definir, Medir, Analizar, Mejorar y Controlar, las organizaciones pueden identificar las causas raíz de las ineficiencias, implementar soluciones basadas en datos y mantener las mejoras a lo largo del tiempo. Adoptar Lean Six Sigma DMAIC no solo fomenta una cultura de mejora continua, sino que también equipa a los equipos con las herramientas y metodologías necesarias para lograr la excelencia operativa y mantener una ventaja competitiva en el dinámico entorno empresarial actual.